Featured designer of the month, Llyn L. Strelau, made one man’s idea a reality with ‘Future Perfect’, an objet d’art symbolising the celebration of the beginning of two lives brought together. The project was a collaboration between the client, technology and the creative talents of six individuals working in concert to realize a symbol of enduring love. Llyn’s business model has always centred around custom design . When working closely with a client to bring their idea to life, it is important to get ‘deep in their psyche’. To understand their needs and ideas, and be able to give what they want, even when they might not know what they want. This creates a rapport between the wearer and the maker , where communication is essential.
At times, though there is a very focused request. The client has very definite ideas of what they wish to have made and then the challenge is to take the concept and make it a reality.
And so it begins. With a love story.
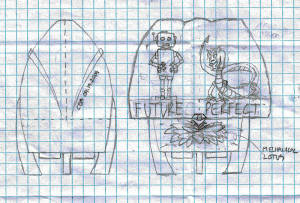
A young professional man, Charlie, met Llyin for a consultation. He wished to have made an engagement gift for his boyfriend, a research physician. It was meant to mark this next stage of their relationship. He brought in a very clear sketch and was very specific about the elements that he wanted in the piece although he had no idea how a piece would actually be crafted.
Llyn’s creativity thrives on these types of challenges, and solving the mechanical problems of Charlie’s piece was a reason to get excited. A lot of Llyn’s work involves narratives, and some of his best and most satisfying pieces tell stories. As a self confessed romantic, Llyn believes that by helping Charlie tell his and David’s story, he contributes to making a dream come true and gets to play a part in the evolution of their relationship.
Personal narrative details
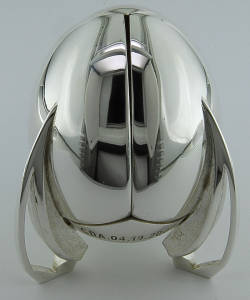
Charlie wanted a small sculpture/object d’art in the form of a retro-style spaceship, which would open to reveal several elements that had significance for the couple and their relationship.
In addition to their motto, ‘FUTURE PERFECT,’ there were to be two passengers aboard: a stylized robot to represent Charlie and an Asian dragon (with five claws on each foot to indicate the dragon’s strength and power) for David, who is from the Far East.
The spaceship’s ‘engine’ compartment was to contain an open lotus flower with a diamond set in the centre above mechanical structures to represent the craft’s engine. The ship’s registration number CDA 04.19.2009 (the date marking the beginning of the ongoing Charlie and David Adventures) was to be engraved on the outside. Although the client’s original sketch showed an egg-shape spacecraft that opened like a three panel screen, Llyn immediately imagined it opening like 3 petals instead. When open, it would reveal the lotus in the base, with the robot in one alcove, the dragon in another, and the ‘Future + Perfect’ legend in the third.
Having an admiration for ‘golden’ age of object d’art, the Imperial Faberge Easter eggs, this project offered an opportunity to get a taste of what the craftsmen of that era were up against.
But the real question was, how to make a concept, someone’s dream, a reality?
Engineering the Spaceship
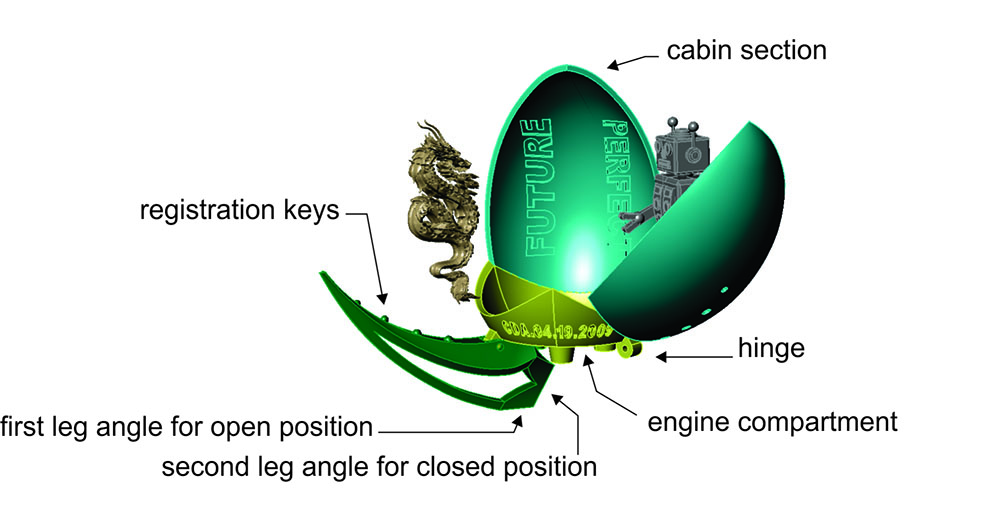
The spaceship’s body was to be approximately the size of an extra-large chicken egg or a Kinder Surprise chocolate egg. Having contemplated using lost ‘chocolate’ casting, a decision was taken to eat the chocolate and use CAD instead.
This would allow a very precise control of all the factors, both mechanical and aesthetic. At the same time, by using calculation and trial and error, would solve some of the mechanical complexities of the project. First, the basic egg shape was modelled using Rail Revolve, trimming the bottom of the egg to leave a flat bottom. Next, three arcs were drawn on the lower surface and used them to first define and then split the ship’s lower engine compartment from the upper cabin section. At this point, since the egg was just a simple shell with no thickness, it had to be bulked up. Using CAD the upper cabin portion was split into three equal pieces, deleted two of them, and then used the single remaining piece for the next steps. The original surface was then offset and the construction curves needed to create new connecting surfaces were drawn.
After joining these surfaces, a cabin section with 2-mm thick walls, heavy enough to be cast, but not too massive to work with was achieved. In the top down viewport, Rotate/Copy was used to duplicate this piece to create the two remaining cabin sections. One of the cabin segments had the words ‘FUTURE + PERFECT’ incised on the inside. Next, the three exhaust ports were added to the bottom of this section and the CDA 04.19.2009 was inset into the outside of the engine compartment.
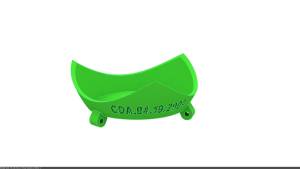
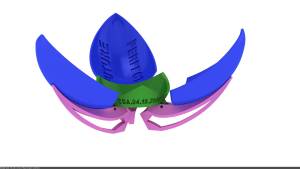
The next step was to model one leg strut. Using the client’s original sketch as the impetus a graceful leg was modelled with an open section and sleek curved surfaces to maintain the aerodynamic appearance. Registration keys were added to the leg and cabin wall to permit accurate alignment in the final assembly steps. Hinge knuckles were modelled to attach to the lower ship section and used Boolean Subtraction to create corresponding sockets in the legs, with holes cut out for the hinge pin. Each leg and its attached cabin section were designed to pivot open from the lower engine compartment. The two angles on the bottom of the legs were chosen specifically so the ship would sit solidly on three legs in both the closed and fully open positions.
Great attention to details was given in this construction stage, and CAD ensured that all the elements would be as accurate as possible.
Engineering the Passengers
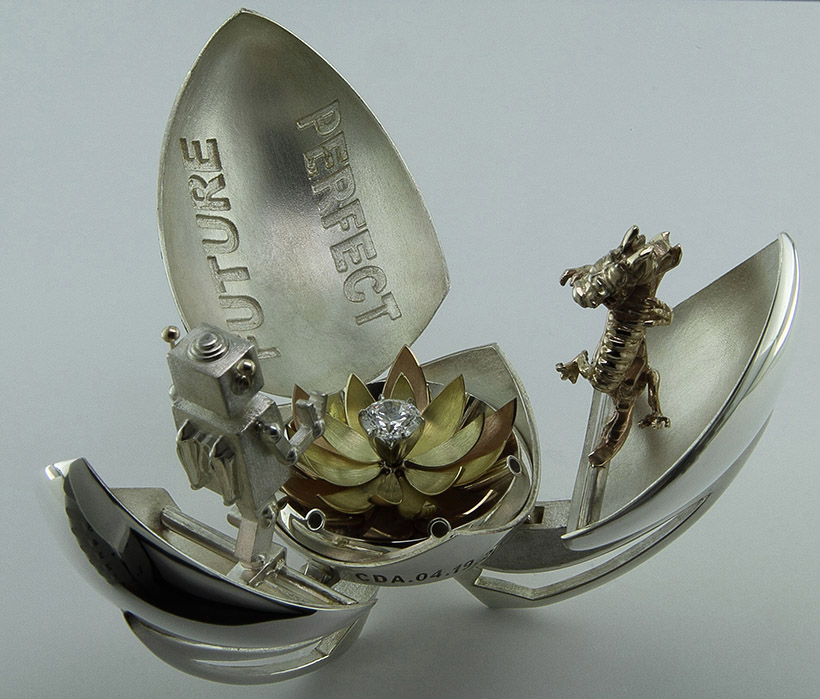
Once the spaceship was designed, it was time to create the two passengers. The robot was modelled in CAD and scaled to fit in its alcove. Its arms are articulated and would be milled in several pieces, then cast in silver and then assembled. The Asian dragon began as a 3-D model purchased from an online library. The model as it came was not in the right pose and required changes to fit with the client’s idea.
Harry Hamill made the changes needed, such as adding five claws to each foot and giving a more sinuous twist of the tail and graceful turn of the head. The robot was given tiny blue sapphire eyes and the dragon received emerald eyes. The two passengers were attached to lengths of silver tubing that pivot on rods spanning the walls of the cabin segment. They can recline during ‘flight’ mode and return to a vertical position when the ship is in its open state.
Fabrication and Metals
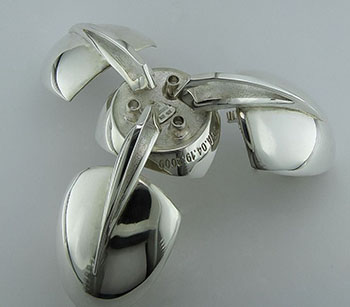
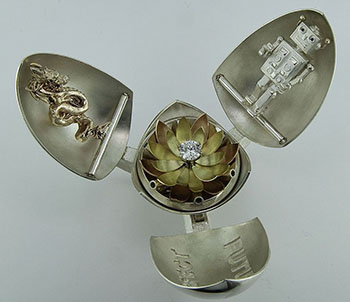
The next step was to hand-fabricate the lotus blossom. The budget was stretched and decided to use three colours of gold to make three layers of petals. Circles of decreasing size were cut from thin sheets of red, yellow, and green gold and dapped to make hemispheres. Initially, the flower’s centre was to be a one-carat diamond, but budgetary restraints nixed this and a cubic zirconia became the temporary replacement. The six-claw, white gold setting holding the stone has a corresponding male bayonet finding, so it can be removed and replaced with a diamond or other gem at a future date.
With the CAD modelling finished, the files were sent to Matthew Todhunter in Edmonton, Alberta, who did a superb job of milling these complicated models. Goldsmith Jerome took over the main construction. The four pieces of the ship’s body , three leg struts, and the robot components were cast in Argentium silver (a proprietary sterling alloy with ‘tarnish-resistant properties). The dragon was cast in yellow gold. The usual bench techniques were used to finish all the components.
Final details
Final finishing and polishing came next. Since the spaceship is meant as a display piece, a wooden case was commissioned for it. John Lavoie, a fine Calgary, Alberta woodworker, created a tiger-wood egg-shape box that also opens like a three-petal flower. Brass pins were fitted into the base to lock into the three exhaust jets on the base of the engine compartment. The client found a glass dome that accommodates the entire assembly, offering the couple a good dust-free environment in which to display the gift.
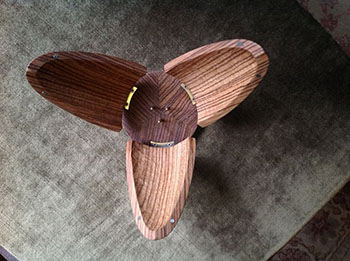
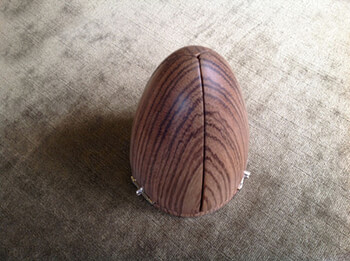
The spaceship was presented and the engagement sealed. A few months later, the couple got married aboard a chartered airplane.
Final words
The Future Perfect tells a story. A deeply personal one, that of Charlie and David, and the beginning of their new Adventure. A story of interpersonal relationship between the maker and the client, where an idea is brought to life mediated by communication and a deep understanding of ones vision. And ultimately, a story of individuals brought together to bring to life a dream, a symbol of love.
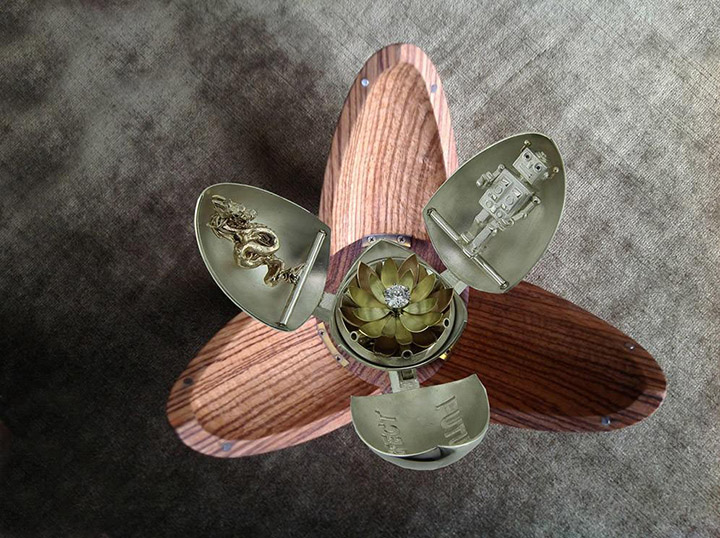