Metals
Page 148
Introduction
The importance of metallurgy throughout history is underlined by our habit of dividing the past into Bronze and Iron ages, with various subdivisions of these. Such convenient chronological nomenclatures imply a greater segmentation of metal use in the past than is strictly true. The periods of usage of different metals and alloys overlapped and there was often a long delay between the first exploitation of a new technology and its adoption by society at large. Egyptian peasants were still harvesting grain with flint-edged sickles 1,ooo years after the pharaoh Pepi I had been immortalised in an over life-size copper statue found at
Hierakonpolis (Cairo JE33034).
We know little of the prospecting habits of the Egyptians, but they were thorough and perhaps systematic in their discovery of metalliferous deposits employing a combination of large-scale state expeditions and smaller prospecting/surveying groups. A graffito by Thuthotep, a’reckoner of gold’ around 2000 BC has been found at the remote Abrak well some 240 kilometres southeast of Aswan (de Bruyn 1955). The prospectors might have lacked geochemical knowledge in the modern sense, but they had a practical understanding of nature. No doubt they could recognise the land formations, rock colours and even flora associated with metal deposits. For example, it has been noted that the pine Pinus halepensis grows particularly abundantly over the copper gossans on Cyprus (Constantinou 1982), while the presence of acacia trees can reflect the presence of copper and lead ores. Possibly, the association of the goddess Hathor with both mines, as at Timna, and with acacia trees is not coincidental. Acacia wood also served as pit props in some Egyptian gold mines – a function which devotees of Hathor might have found reassuring.
In the ancient Near East, ores were generally treated at or near the mines; it is easier to transport and keep a tally of ingots than bulkier raw materials. Nevertheless, the availability of fuel would dictate the best option for treatment locality. The urban craftsmen were probably far better acquainted with associated craft activities such as faience and
glass manufacture than ore recovery and mining processes.However we do not know the economic or other factors that decided which ores should be locally treated near the mines to produce metals or which if any might be transported for use in the pigment and glaze industries.
Our understanding of ancient Egyptian metals comes from the careful study of surviving examples using, increasingly, the analysis and internal study made possible by technological advances. To date, thousands of analyses of Egyptian metals have been published (e.g. Riederer 1978b, 1981, 1982, 1983, 1984, 1988; Lucas 1962; Fleming and Crowfoot-Payne 1979). A good summary of earlier analyses is given by Riederer (1982) and an overall summary of results is provided by Kaczmarczyk and Hedges (1983). There are also numerous other analyses scattered in the conservation and scientific literature, while a huge number undertaken by museums around the world remain unpublished. Most of these analyses have been carried out on supposed Late Period copper alloy objects. Garland noted that
Amongst archaeologists it is the practice to assign any non-ferrous metal object not found under known and convincing circumstances or not bearing marks by which they may be dated … to the Saitic period, generally the 26th Dynasty. (Garland and Bannister 1927= 83)
This tradition is still alive and well. Firm chronological distinction will not be possible until analysis of metal finds becomes as standard a practice in Egyptology as it is in some other archaeological fields. Analysis is now an integral and useful part of archaeology and art history. For example, Riederer, on the basis of his various analyses of over 1,2oo Egyptian copper alloy objects, noted that composition sometimes seemed to vary with subject (Riederer 1978b, 1981, 1982, 1983, 1984, 1988). This ties in with Roeder’s earlier observation that forms or poses of deity figures tended to differ from place to place within Egypt (Roeder 1956). This is understandable. If the statuettes were usually made at the local temples, their attributes and poses might be expected to replicate those of the cult statues then in use there, while their compositions would reflect
Page 149
the traditions of, and constraints on, the local metalworkers as well as aesthetic and colour considerations.
Our knowledge of ancient sources of ores and other natural products is helped by the published geological studies of Egypt, including much undertaken since the Second World War on metal ore distribution and geochemistry. The reader is thus directed to the specialist geological literature, starting with el-Baz’s annotated bibliography (el-Baz 1984). John Harris’ 1962 revision of Alfred Lucas’ fundamental work Ancient Egyptian Materials Industries is, of course, still invaluable and the reader is directed to the older works referenced there, in particular to those relating to excavation reports and ancient documentary sources (Lucas 1962).
Antimony
Antimony is a light, bright, white metal, not unlike silver in appearance, but it is brittle and better suited to casting, not mechanical working. The use of metallic antimony in ancient Egypt has been reported, but such instances were largely discredited by Lucas on the basis of visual study and, where feasible, analysis (Lucas 1962: 195-9). Thus we can now exclude such supposed examples as the ‘antimony powder’ said to have been found in Tutankhamun’s tomb and the ‘antimony plating’ on an Old Kingdom vessel. Readers are directed to Lucas’ comments and can also note that Meyers’ more recent re-analysis of the ‘antimony plated’ vessel confirmed that the surface layer was indeed actually arsenic due, almost certainly, to natural surface enrichment (Lucas 1962: 198; Smith 1970: 102, n. 5).
Tne only confirmed examples of metallic antimony from ancient Egypt published to date are the small beads, probably of native antimony, of Third Intermediate Period date which were found by Petrie at Lahun and analysed by Gladstone (Lucas 1962; Garland and Bannister I92T 32). The identification is supported by the existence of occasional excavated (and analysed) finds of metallic antimony outside Egypt – in Western Asia, Transcaucasia and Italy (Caley 1964: 135-6; Moorey I99+ 241-2). The Egyptian beads were probably imports since antimony ores occur as little more than minute traces in Egypt.
Some Iron-Age beads from Tell el-Fara in Israel are described by Dayton (1978: 450) as tin:antimony alloys with about 66 per cent tin and 33 per cent antimony. Although antimony has not yet been found as a principal component in any ancient Egyptian alloys, we might well expect other examples of metallic antimony and antimony-rich alloys to be identified as analysis becomes more routine. As a caveat, however, we can note that objects made of antimony alloys occasionally appear in collections that are modern fakes made of easy-to-cast ‘type-metal’.
Antimony is common in small amounts in ancient copper alloy objects (usually under about 1 per cent) and as a trace element in lead. It is also found as an ingredient in
Egyptian faience from the time of Thutrnose III and in glass from about the Amarna period onwards (Kaczmarczyk and Hedges 1983: 98). An antimony compound was also used as an occasional eye-paint in Egypt from the Amarna period onwards, but this was far less common than has generally been supposed- a state of affairs seemingly also true in Mesopotamia (Lucas 1962: 196-9; Moorey 1994: 241). The evidence suggests that antimony, as ore or native metal, was reaching Egypt from the New Kingdom onwards, and was perhaps sometimes confusedwith tin.
Bronze see copper and copper alloys
Electrum see gold and electrum
Copper and copper alloys
Copper is a pinkish-yellow metal that occurs native- that is in metallic form – or, far more commonly, as coppercontaining ores from which the copper can be extracted by procedures termed smelting. Copper-bearing deposits can contain copper ores of varying complexity and purity and some native copper. Apart from metallurgy, there were a myriad of uses for copper and copper ores in ancient Egypt: in medicines (Weser 198T 189-94), as pigments (see pp.153, 154, 156 and Chapter 4, this volume) and as colouring agents in glazes and glass (seep. 156-7 and Chapters 7 and 8, this volume).
Occurrence and retrieval
The main copper-producing regions accessible to the ancient Egyptians were the Eastern Desert and the Sinai, including the Serabit el-Khadim region in the southwest and Timna in the Wadi Arabah, now part of Israel. The epigraphic evidence only refers to the turquoise found at Serabit el-Khadim, but the reported remains of tuye’res, moulds, crucibles and casting installations suggest local ore treatment (Beit-Arieh 1985: 89-116). Copper slags, ores, crucibles, ingot moulds and other working detritus of Old and Middle Kingdom date have also been found at Wadi Magharah, some twenty kilometres southwest of Serabit el-Khadim. However, it is possible that this was more a treatment centre for ores from the surrounding region than a major mining area (Petrie 1906: 51-2; Lucas 1962: 202-4; Beit-Arieh 1981: 95-127). In view of the turquoise-biased epigraphic material, it is difficult to determine the relative extents to which mining in the Serabit el-Khadimj/Magharah area was directed at the turquoise (see Chapter 2, this volume, for discussion of the implications of the term mJkJt) or at the copper. However, we can note that the scale of imperial turquoise exploitation in Sinai in the New Kingdom contrasts with the sparse surviving examples of its use in Egyptian jewellery. It is difficult to believe that jewellery was its primary employment. The use of ground turquoise in glaze-making had been suggested
Page 150
by Petrie but rejected by Lucas. Turquoise is an aluminium phosphate. Aluminium is commonly found in glazes due to its presence in sand. However, traces of phosphorus are also found in some Egyptian glazes but have not so far been satisfactorily explained (Lucas 1962: 186-7)- Representations of turquoise at the mining sites in the form of cones, apparently of powder, not nuggets or blocks, tend to suggest non-jewellery use.
Our best evidence of ancient copper exploitation in Sinai comes from the Timna mines and smelting sites which
have now been excavated and studied in considerable detail. This mining area reveals the recovery and local smelting of copper ores from the fourth millennium BC onwards and the gradual development of the metallurgical processes employed. Traces of manganese in a Predynastic axe and protodynastic copper bands have been taken as evidence that the copper came from Sinai (Lucas 1962: 209). There is little evidence for continued exploitation of the Sinai mines during the First Intermediate Period, but mining was re-started in the Eleventh Dynasty and became extensive in the Twelfth Dynasty, with an increasing documentary record (Mellado 1995). Copper-mining activity at Timna appears to have reached its peak during the Nineteenth
and Twentieth Dynasties and represents the largestscale Egyptian copper-mining enterprise so far discovered
(Shaw 1998). The Timna mines were essentially a series of cylindrical shafts which linked underground galleries. According to Craddock:
The mines were small, shallow and, although linked underground, display little evidence of any overall mining strategy, or of any knowledge of the possibilities of ventilation or drainage. (Craddock 1995: 69)
Timna has been associated with the New Kingdom copper mines at Atika mentioned in Papyrus Harris (Levene
1998). Workings at Timna appear to have ceased abruptly in the time ofRameses V. Strangely, there is no evidence so far for any exploitation of the Timna mines in the Late Period – the period when the production of copper statuettes and the like in Egypt increased exponentially. For a
general survey of the Timna mines see Rothenberg (1972).
In Egypt itself, copper ores occur along almost the entire length of the Eastern Desert into Nubia. There is a cluster of copper deposits in the Eastern Desert inland from Safaga, and between Safaga and Quseir there are copper ores with various lead, zinc and nickel associations (Nassim 1949: 143-50). The extent of ancient workings is still largely unknown, but the lead and zinc contents of some of the ores might suggest an origin for the high lead levels in copper glazes from Elkab in the Old and Middle Kingdoms (Kaczmarczyk and Hedges 1983: 235). Copper mines of ancient but uncertain date at el-AtawijWadi Sitra (due east of Luxor) might have supplied workshops within the temple complexes at Thebes, where workers carried out such ambitious commissions as the casting of the doors for the temple of Amun at Karnak (as represented in the Eighteenth-Dynasty Theban tomb of Rekhmira, TT1oo; Davies 1943; see Fig. 6.1). The Ptolemaic bronze foundry recently found at the funerary temple of Seti I at Thebes might well come at the end of a long tradition of temple-based metalworking in the area (Scheel 1989: 41).
The Hammash area, north east of Aswan, has chacopyrite (copperjiron sulphide) ores with some associated gold. The ancient gold and copper workings in this region include some which date back to the Middle Kingdom, if not earlier (Klemm and Klemm 1994). On the basis of analyses of copper-containing glazes, Kaczmarczyk and Hedges (1983) have recently suggested that the southern Eastern Desert was already being exploited in the Middle Kingdom, and perhaps even as early as the First Dynasty. Simple ores such as malachite, cuprite and atacamite (with the deeper deposits of sulphides with zinc, lead and silver admixtures) also occur at Samiuki in the Eastern Desert, not far from Ras Banas (Anwar 1964: 89-94). Lucas, following Hume, called the mines in this area ‘the most important deposits of copper yet discovered in Egypt’, and describes the extensive underground workings and the general copper recovery detritus such as ore crushers and slag. According to Lucas (1962: 206-8), the mine at Abu Seyal was ‘worked extensively’ in ancient
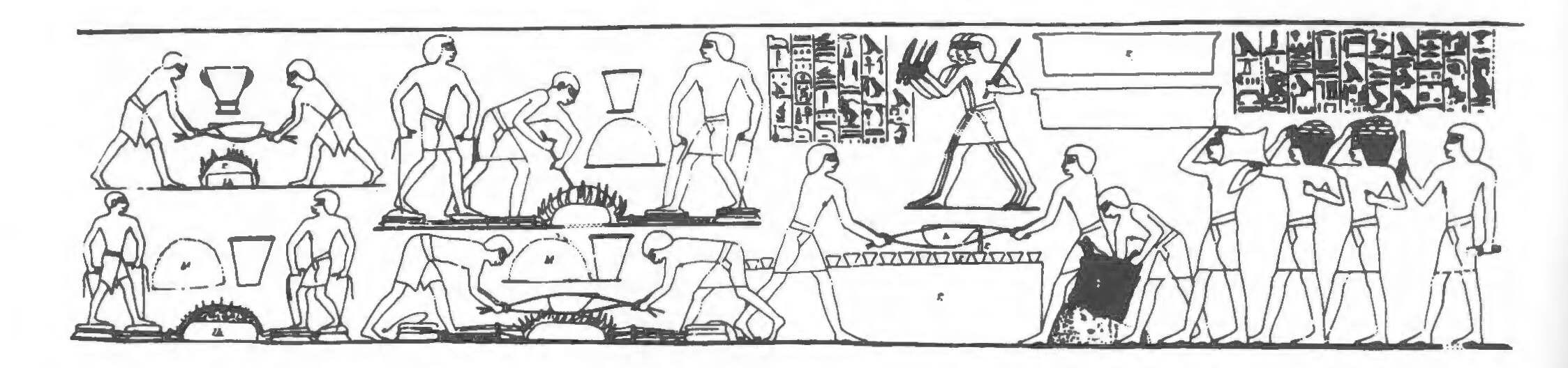
Page 151
times. It has been suggested that at least some of the ore from this area was treated at Quban, where there is abundant slag. A stele from southeast of Aswan refers to the official Hor who had been instructed to collect ‘copper from the land of Nubia’ during the Twelfth Dynasty (Lucas I962: 209).
The association of gold and copper ores is not unusual in the Eastern Desert and Nubia. The ore samples found at the Old Kingdom smelting site at Buhen are primarily malachite with a low iron content, but they have been reported to have a remarkably high gold content (el-Gayar and Jones I 9 8 9 b). The copper derived from these ores is also reported to have included gold particles, but – in view of the ready solubility of gold in copper- these results have been questioned (Craddock and Giumlia-Mair I993)· The Abu Seyal ore, however, appears to be different from that smelted at Buhen and a more southern source for the latter is likely (el-Gayar and Jones I989a: 3I-40).
Literary references to the import of copper into Egypt from the north seem to occur first during the New Kingdom (Lucas I962: 209), and some of this copper undoubtedly originated in Cyprus. Oxhide ingots – a form characteristic of (but not unique to) Cypriot copper exports-are depicted in the tomb of the Eighteenth-Dynasty vizier Rekhmira at Thebes (TTioo). In addition, the famous wreck from Ulu Burun (Turkey) contained copper which is assumed to have been traded from Cyprus to Egypt in the fourteenth century BC (Bass I986: 269).
Copper and its alloys
Neither native copper nor the copper produced by smelting ores are roo per cent pure copper. They always contain a variety of other metallic impurities, the nature and amounts of which can reflect the geochemistry of the deposit, the metallurgical processes used in extraction and smelting, and the nature and purity of any intentional alloying metals. The major and minor elemental composition of copper or copper-alloy objects can thus provide potential chronological and geographical information, including evidence for authenticity.
The term ‘copper alloy’ as used here covers a wide range of alloys in which the predominant metal is copper. In the past the term ‘bronze’ was often used indiscriminately to cover all copper alloys and even copper alone, but the term ‘bronze’ is more correctly limited to those alloys which are predominantly copper and tin.
Copper
Some of the earliest examples of copper objects from Egypt – simple, flimsy ornaments and implements from as early as the Badarian period – might possibly have been made from native copper, i.e. copper found in nature in metallic form, not as ores. However the availability of native copper in early Egypt might well have been overstated in the past. For example an Early Dynastic copper chisel found in Nubia has a small silver and gold content which led to its
identification as native copper. Lucas, however, felt that it was highly unlikely that such a comparatively large object could be of native copper. He proposed the use of copper ore with a small precious metal association (Lucas I962: 200-I} -a view now supported by the proved association of copper and gold in some ores as noted above.
The simple ‘oxide’ copper ore minerals, such as malachite and azurite (both copper carbonates), have bright colours that would attract prospectors and require only fairly elementary smelting procedures. Although even for the simplest ores some pre-treatment, such as hand sorting and crushing ‘benefication’, would have been important to maximise the yield (Doonan I994: 84-97). Relatively low temperatures and initially simple crucibles with blowpipes, later small furnaces, would suffice. Experiments have shown that copper can be smelted in clay crucibles with a bank of three or more blowpipes. Up to 90 per cent recovery is possible with simple oxide ores such a malachite and no slag is produced (Craddock I99r 126-7). The large quantities of crucible fragments, malachite and atacamite and copper priUs at Buhen, but no slag, have been taken to indicate crucible smelting of copper here in the Early Dynastic Period (el-Gayar and Jones I989a, I989b; Craddock I995: I3Q-I).
If we accept that some impurities in the copper, such as arsenic or nickel, are indicative of smelted copper ores, not native copper, the introduction of smelted copper, albeit fairly impure, must have occurred in Egypt by about 4000 BC. In Egypt the low iron levels (average o.o3 per cent) that we see in some of the earlier Predynastic and First Dynasty Egyptian copper alloy objects probably reflect the use of primitive smelting operations using crucible furnaces.
More efficient production, and the ability to exploit more complex and lower grade ores, required higher temperatures and a procedure termed ‘fluxing’ – the presence or addition of materials to aid the melting and separation of the copper. Iron oxide was the general flux. The smelting of oxide copper ores with iron oxide results in the formation of a mass of mainly iron-minerals, the ‘slag’, and the reduced copper. This copper is either produced as small priUs which are retrieved by crushing the mixed mass of cinders and slag, or, if higher temperatures over longer periods are obtainable, will form a puddle in the base of the furnace which will cool to give a plano-convex or bun ingot. Craddock and Meeks (I98T I87-204) have described the simplest type of early copper-smelting shaft furnace as ‘probably the size and shape of a small upturned bucket but lacking its bottom.’ We might assume that bag bellows superceded blowpipes for copper-smelting. However, there is little certain evidence for bellows from Egypt until pot bellows appear in the Middle Kingdom (seep. I57)· Tylecote calculated that the plano-convex ingots produced at Timna in the more sophisticated shaft furnaces of the New Kingdom weighed between about
Page 152
three or four kilograms a slightly higher estimate than Merkel (1995: 22).
Simple fluxing with slag production was in use at Timna in Sinai by the end of the fourth millennium BC and was soon fairly universal in the Eastern Mediterranean world. Its introduction into Egypt, as evidenced by a sharp rise in iron levels (to an average of about 0.33 per cent) seems to have occurred during the Second Dynasty (Craddock 1985; Craddock and Meeks 1987: 187-204; Cowell 1987; Craddock 1995: 137-40). Recent investigation of slags from Bir Nasib in Sinai show the production of unfluxed copper in Predynastic times and the use of iron ore fluxes by some unspecified time during the Old Kingdom (el-Gayar and Rothenberg 1998; Craddock 1995: 130—I).
The copper produced at the Old Kingdom smelting site at Buhen has an average iron content around 0.5 per cent (el-Gayar and Jones 1989b) and the over-life-size Sixth-Dynasty statue of Pepi I is, according to what is probably the most reliable analysis to date (Desch 1928), almost pure copper with 0.7 per cent iron, enough to indicate a true fluxing process, and LI per cent nickel. Gladstone and Lucas also analysed samples of the Pepi statue and both reported high purity copper and no tin (Lucas 1962: 214).
More efficient copper production was possible when the slag could be run off while molten. ‘Tapped-slag’ furnaces of this type can probably be dated in the Sinai to the time of the middle to late New Kingdom. It is noteworthy that the average iron levels in Egyptian copper alloy objects drops to around 0.14 per cent by the Late New Kingdom. There are various possible explanations for this. It could reflect the introduction of tapped slag furnaces, the switch to sulphide rather than oxide ores, or, possibly, the employment of manganese rather than iron fluxes utilising the extensive manganese mineral deposits in those areas (Rothenberg 1972: 232; Bachmann 1980: 103-34).
The introduction of more efficient copper-production methods could help explain the exponential increase in cast copper alloy objects during the Third Intermediate Period and Late Period. Sulphide ores were undoubtedly smelted by this time, although the oxide ores, when available, were also still utilised. The smelting of sulphide ores will produce copper with, in theory, lesser amounts of trace elements such as arsenic, antimony and bismuth. For sulphide ores, prior roasting is required and silica, not simply iron oxide, usually has to be present as a flux. The fact that concertina bellows appear to have been introduced in the Near East in the first millennium BC might have aided copper as well as iron production (Craddock 1995: 181-3).
Pure, or near-pure, copper is not easy to cast because it is prone to gas bubbles and tends to shrink, thus producing poor-definition, porous castings. Nevertheless, some surviving Egyptian objects of high purity copper dating right up to the New Kingdom show that the smiths were able to cope with consummate skill.
When first smelted some of the iron from the flux will enter the copper which will thus contain several per cent of iron — as seen in Late Bronze Age copper finds from Timna. Levels of iron up to 1 or 2 per cent are not uncommon in Egyptian copper alloy objects, but higher iron levels — up to io per cent or so can enter during smelting — make the copper almost impossible to cast or hammer. The copper has to be refined to remove at least the majority of the iron. It is quite easy to bring the iron contents down to around 0.5 per cent by simply melting the copper and scooping off the oxidised impurities from the surface of the melt. An ingot found in the Wadi Araba, some way from Timna, shows that ingots left the smelting sites in unrefined state.
Copper objects with several per cent iron occur sporadically right through Egyptian history. Examples include a Fifth-Dynasty amulet (Brunton et al. 1927: 69) with around 6.5 per cent iron, and a fine, hollow-cast head from a statuette of a Ramesside pharaoh with around 95 per cent copper, 2 per cent lead and 2 per cent iron (Schoske and Wildung 1992: 221-2). We can probably assume such iron contents are fortuitous. A copper cat in Hamburg has been reported to contain almost 12 per cent iron (Riederer 1988: 7). Such an alloy would be extremely difficult to cast and perhaps needs verification — the possibility of contamination of iron from another object or iron wire core supports (see p. 159) should be borne in mind. However, we can note the intentional copper alloys with up to 20 per cent or more iron met with in Iron-Age Italy and elsewhere (Craddock and Meeks 1987: 187-204).
Nickel is a common impurity in ancient copper alloy objects but usually under about 1 per cent. Higher nickel contents are most typically found in zinc-containing copper and thus seldom encountered in Dynastic Egyptian objects. Other trace elements in ancient Egyptian copper and copper alloys include bismuth and cobalt.
Copper - arsenic alloys
Arsenic is present in many ore types and there are at least traces of arsenic in most ancient Egyptian copper and copper alloy objects. Arsenic presence results in the production of wrought copper of far greater hardness — a vital property for implements and weapons — and also greatly facilitates casting by causing the molten metal to flow more easily. The convention is that copper objects with more than about I per cent arsenic are regarded as representing the deliberate use of arsenic-rich copper ores or the intentional combining of arsenic and copper ores (Moorey 1994: 242). Almost certainly the higher arsenic levels which appear during the Old Kingdom were not fortuitous (Kaczmarczyk and Hedges 1983: 73). Up to 7 per cent was found in axes in the British Museum (Cowell 1987). Analysis of blue copper-based pigments from more than Ho well-dated Egyptian tombs not only confirms the view that this pigment was made from scrap or by-product copper — as Vitruvius (De Architeaura VII, Ch. XI, I; see Morgan 1914) later states — but also provides corroborating chronological information.
Page 153
Arsenic is found first in copper-based pigments in the Fifth Dynasty (el-Goresy et a1.1998).
The frequent association of high arsenic with low levels of other impurities is an argument in favour of intentional additions rather than the use of an enriched ore type. We might expect intentional use of arsenic-rich copper ores from an early period followed in time by deliberate additions of arsenic ores to copper or copper ores. However, there is no way to make a definite distinction using current analytical methods.
Analyses have seldom revealed any definite discernible difference between arsenic content and intended use — we would expect low arsenic levels in objects that would benefit from a soft rather than a hard alloy in manufacture. On the other hand, the attractive silver colour of arsenic-rich copper was one motive for its use, regardless of the function or mode of manufacture of the object.
Arsenic is still present in noticeable amounts in a handful of Egyptian copper and copper alloys in the New Kingdom. It is found in copper-based pigments up to the time of Hatshepsut (el-Goresy et al. 1998). Arsenic levels in post-New Kingdom copper alloy are typically less than about per cent. When higher levels occur they are presumably, in the main, fortuitous. However, Riederer’s analyses (Riederer 1978b, 1981, 1982, 1983, 1984, 1988) show that Late Period cat figurines and cat heads appear to have high arsenic contents more often than might be expected by pure chance. Schorsch (1988) has also referred to a Late Period cat head with a noticeable arsenic content. The two highest arsenic levels recorded by Riederer in post-New Kingdom objects (4.13 per cent and 6.39 per cent) are both in figures of the young god Harpocrates and an intentional colour choice seems possible, given that children were rendered with paler skin than adults in Egyptian art.
It is perhaps relevant that arsenic-based pigment (orpiment — arsenic sulphide) only seems to have come into use in Egypt during the Amarna Period, the very time at which the use of arsenic in copper alloys began to wane. There is no evidence that the ancient Egyptians knew arsenic in metallic form — a state of affairs paralleled in Mesopotamia (Moorey 1994: 240), although supposed examples have been cited from the ancient world.
Antimony is a frequent associate of arsenic and also appears as a trace element in most Egyptian copper alloy objects. Antimony has a similar hardening effect to that of arsenic on copper, but the intentional addition of antimony is unlikely in Egypt until the New Kingdom, after which it might have been used on occasion — perhaps confused with tin. Ancient Egyptian copper or copper alloy objects with over about r per cent antimony are unusual, but occasional levels up to almost 4 per cent occur even in the Late Period. Interestingly, Riederer’s analyses include only five examples with over 2.5 per cent antimony — two of these are the high-arsenic Harpocrates figures mentioned above.
Copper- tin alloys
When copper is alloyed with tin there is a noticeable increase in the hardness and potential sharpness of copper alloy tools and weapons. The melting temperature drops from 1,083 °C (pure copper) to 1,005 °C for copper with 10 per cent tin. Tin also greatly increases the fluidity of the molten metal, thus facilitating casting. The effects are not dissimilar to those produced by arsenic additions, but are more dramatic and without the very real toxicity hazards. Arsenic additions, intentional or not, permit better casting than pure copper, but the large-scale production of fine-quality castings might have had to await the introduction of copper—tin alloys.
As with arsenic, around r per cent tin is usually taken to be the dividing line between accidental and deliberate presence. The deliberate addition of tin (though presumably in the form of an ore, not metallic tin) to copper had occurred in some parts of the Near East by 3000 BC. Tin levels of over r per cent have been found in several Early Dynastic objects with the highest reported levels to date being 7 per cent and 9 per cent respectively in a ewer and basin from the tomb of the Second-Dynasty king Khasekhemwy (Cowell 1987; Kaczmarczyk and Hedges 1983: 78). We can also note that Berthelot (1895) found almost 6 per cent tin in a Sixth-Dynasty vessel. Deliberate copper—tin alloys (true `bronzes’) were still the minority in the Middle Kingdom. Examples include the superb Middle Kingdom hollow-cast figure of a man, now in the Louvre (E27153), which contains around 5 per cent tin and about 1 per cent arsenic (Delange 1987). Berthelot noted just over 16 per cent tin in a Twelfth-Dynasty bracelet fragment from the Dahshur treasure (Berthelot 1895).
Copper—tin alloys still had to share the stage with copper and copper—arsenic alloys in the New Kingdom. A Thutmose IV statuette in the British Museum (BM EA64564) is almost pure copper (Craddock 1985), and Lucas remarked that there was still more copper than bronze in the tomb of Tutankhamun (Lucas 1962: 220). We can also note that tin first occurs in copper-based pigments during the reign of Thutmose III (el-Goresy et al. 1995: 31). From the Ramesside period onwards, tin is present in the majority of copper alloy objects. Interestingly, the arsenic content of copper alloy objects drops dramatically from the New Kingdom on, and is rare after that time. The way in which tin (and lead —see p. 154) ousts arsenic at this time is matched elsewhere in the Old World and is a strong argument that earlier arsenic additions were intentional. Analyses of Egyptian glazes also show that tin became far more readily available during the New Kingdom. This agrees with the suggestion that the additions to copper alloys were now of metallic tin, not tin ores. This could also explain the appearance of other unusual tin alloys in the New Kingdom (see p. 171 under tin). The source or sources of the tin, however, are still uncertain.
Page 154
The majority of Egyptian bronzes have up to around ro per cent tin, as is generally typical in antiquity, but there are occasionally higher levels though very rarely over about 16 per cent. There are some possible chronological variations that deserve further research. For example, there appears to be a dip in average tin content in Third Intermediate Period objects, while Ptolemaic and Roman-period objects more frequently have higher tin levels than hitherto (Kaczmarczyk and Hedges 1983: 90). High tin contents will produce a copper alloy with a silvery colour, indeed a Late Period menit in the Fitzwilliam Museum, Cambridge (EGA.54.- 1949) is of over 90 per cent copper, while its ‘Electrum’ inlay is actually composed of a copper–tin alloy with just over 20 per cent tin.
Correlations between object function and composition also deserve further study. It is only to be expected that there should be distinctions between, say, weapons and decorative objects due to working properties of the alloys (i.e. some alloys forming better castings, and some able to be hammered and worked to provide sharper, more durable edges). However, we can also suspect a far wider range of less obvious distinctions, some perhaps based on colour or susceptibility to surface treatments, others due to ‘symbolic’ reasons. For example, the programme of analyses on tools and weapons in the British Museum revealed that model tools could match the composition of their functional counterparts, although the high purity copper of three models of agricultural tools from Tutankhamun’s tomb and of eleven models of tools and weapons from the Fifth Dynasty suggest that this was not always true (Coghlan 1975: 64-7; Maddin et al. 1984: 33-41). The potential colour relationships are particularly interesting. For example, among Riederer’s recent analysis of some 1,200 Egyptian copper alloy objects, only three statuettes have over 16 per cent tin – all three are figures of the child-god Harpocrates. This suggestion of a link between a pale alloy (see also copper arsenic and antimony alloys p. 152-3) and the rendering of a child-god’s skin, raises the question about the factors involved in alloy choice. Sadly, again, far too few excavated copper alloy objects are properly studied, while those currently in collections have often undergone extensive and frequently poorly recorded cleaning and conservation treatments which will have often destroyed much of the evidence for original surface.
In this context we can note recent analyses of New Kingdom stirrup-shaped finger rings, induding unpublished analyses by the present writer of examples in the Fitzwilliam Museum, which show that they are typically true bronzes with 8-10 per cent tin (see Giveon 1977: 66-70). It must be assumed that such objects were produced with, or soon obtained in use, polished metal surfaces. The electrum-like colour of the alloy would resemble that of the similarly shaped gold alloy rings. That these rings were intended for use in life is proved by the considerable degree of ancient wear on some examples.
One conundrum is the existence of copper objects containing between o.i per cent and 1 per cent tin. Mixed copper–tin ores are rare, and analytical evidence from Timna in Sinai from samples from various stages in the copper recovery process suggest that even such minute amounts might well have been additions. Such low levels would have no noticeable effect on the final hardness or working properties of the metal, but they might have facilitated casting by deoxidising the alloy (Craddock 1980).
Copper alloys with lead
Between r and 3 per cent lead in a copper alloy will facilitate casting without detracting from the strength of the alloy. Thus while up to about 2 per cent lead can be fortuitous, lead levels as low as 1 per cent might sometimes be deliberate. This is indicated by an apparent correlation of lead content with copper–tin rather than copper–arsenic alloys prior to the Late New Kingdom (Cowell 1987). Early examples include the Second-Dynasty copper–tin alloy ewer and basin mentioned above which both contain over r per cent lead.
Generally speaking, the addition of lead to copper alloys is rare before the Middle Kingdom and lead levels over about 2 per cent are rare prior to the late New Kingdom. The 16 per cent lead recorded long ago by Flight as being present in a Fourth-Dynasty copper alloy statuette is presumably a case of mistaken dating (see Riederer 1982: table I). However, firstly Phillips did report 8.5 per cent lead in an Eleventh-Dynasty object (see Riederer 1982: table r), and secondly two Eleventh-Dynasty copper alloy cylinder seals of Mentuhotep, now in the Louvre, have been analysed and shown to have a high lead content (Vandier 1968). It has been stated that an inlaid crocodile statuette in Munich (which originated with the same dealer as the Louvre/Ortiz Middle Kingdom copper alloy statues and is thus assumed to be part of the same Middle Kingdom find) is a leaded alloy (Scheel 1989: 41). However, the contrary view (Delange 1987) has now been shown to be correct (Giumlia-Mair 1996). A leaded alloy figure in the Louvre described as of Second Intermediate Period date (Delange 1987: 176-7) is perhaps, on stylistic criteria, a later archaising work.
The deliberate larger scale addition of lead to copper alloys is generally defined as marking the transition to the Late Bronze Age in archaeological terms. High lead levels –up to 25 per cent or more in some cases – lower the melting point of copper, increase the fluidity of the molten metal and reduce porosity. Around 25 per cent lead can lower the melting temperature of a copper–tin alloy to less than Boo °C. Lead thus facilitated the production of the ubiquitous cast copper alloy objects of the first half of the first millennium BC, but was an unwanted presence in alloys intended for edged tools or weapons.
There are perhaps occasional high-lead objects from the Eighteenth Dynasty, such as a vase with almost 15 per cent lead published by Craddock (I985), assuming that the dating of the object is secure.
Page 155
However, it can generally be assumed that the introduction of lead as a major component of copper took place in the Nineteenth Dynasty. Apparently 25 per cent lead was present in a Nineteenth-Dynasty Osiris figure analysed long ago by Rathgen (see Riederer 1982: table’) and Craddock (1985) has published a Twentieth-Dynasty shabti figure containing about 5 per cent lead. We can note, as a parallel, that the deliberate use of lead compounds in glaze manufacture is a New Kingdom innovation (see Chapter 8, this volume) and, more precisely, lead only became a major component in Egyptian copper-based pigments between the time of Seti II and Tausret in the Nineteenth Dynasty (el-Goresy et at. 1998: 31).
In the Third Intermediate Period, copper alloy lead levels are still usually under 5 per cent and the thinner-walled, and more precise hollow castings appear to be tin-bronzes with minimal lead, although copper lead alloys, some with over 20 per cent lead, were becoming more common. However, high lead content is typically a Late Period phenomenon that continued into the Ptolemaic period, when over 20 per cent is not unusual, and over 3o per cent is reported in some instances.
A lead content in copper alloys, even if small, can permit characterisation of the lead isotopes present and thus, potentially, perhaps indicate actual sources of the lead. In recent years there has been much work carried out on lead isotopes in ancient objects in general (see under lead and silver pp. 168, 170), including Egyptian copper alloy objects (Fleming 1982: 65-9), but the validity of the technique is still under review. It should also be noted that lead in a copper alloy can possibly derive from the fluxes used in the smelting process (Rothenberg 1972: 237).
Copper - zinc alloys
Several of the Eastern Desert copper ores contain zinc (sometimes making up a considerable proportion), but these ores would seldom produce an alloy with more than or 2 per cent of zinc. Early use of such mixed ores might explain such objects as a copper pin from a Predynastic grave (no. 218) at Naqada which is stated to contain around 2 per cent zinc and 1 or 2 per cent nickel (Baumgartel 1960: 18).
In Egypt the only pre-Roman use of deliberate copper—zinc alloys — what we term gun metals or brasses — might have been for some late Ptolemaic statuettes and small ornaments. Even some of these, such as some figurines in the so-called `Alexandrine’ idiom, are possibly of early Roman rather than Ptolemaic date. Supposed copper alloy objects or components from Dynastic Egypt with more than 2 or 3 per cent zinc are generally intrusive in the excavation or fake. For an example of the latter see Russmann (1981: 149-56). Here the uraeus was a modern zinc-containing alloy, the statuette itselfwas a leaded tin-bronze and ancient.
The manufacture of the objects
Copper working ‘factories’ have now been identified in various parts of Egypt. Here the ingots from the mines, scrap or imported metal were transformed into a plethora of implements, weapons and ornaments for a temple, royal, secular or dead clientele (Scheel 1989).
For example, a major copper-alloy working centre at Qantir, ancient Piramesse, in the Eastern Delta has recently been discovered (Pusch 199o). The excavations have revealed a massive late Eighteenth- to early Nineteenth-Dynasty metal working site covering over 30,000 square metres (see Figs 6.2 and 6.3). Tangible evidence includes crucibles, tuyeres, moulds, waste, slag and other metal-working tools. This was a centre that included very large-scale copper alloy casting and, perhaps, parallel craft industries. The presence of foreign, including Hittite, armour, weaponry and tools points to foreign craftsmen. The workshop methods revealed can be compared with those depicted in tomb-paintings of the period and with further study of this remarkable site we will undoubtedly gain a far greater understanding of the Egyptian metal-working industry.
There is a wide repertoire of metal-working scenes in tombs (Scheel 1989). For example, the Fifth-Dynasty tomb of Wepemnofret (called Wep) at Giza has scenes showing copper-working (Weinstein 1974: 23-5). These include melting and pouring and, most interestingly, what is probably the earliest reference to annealing with the hieroglyphic caption ‘There is no cracking (?) if it is heated excellently’. Annealing is the heating process used to soften, and make more workable, metal that has become hard and brittle due to the build up of stresses during shaping.
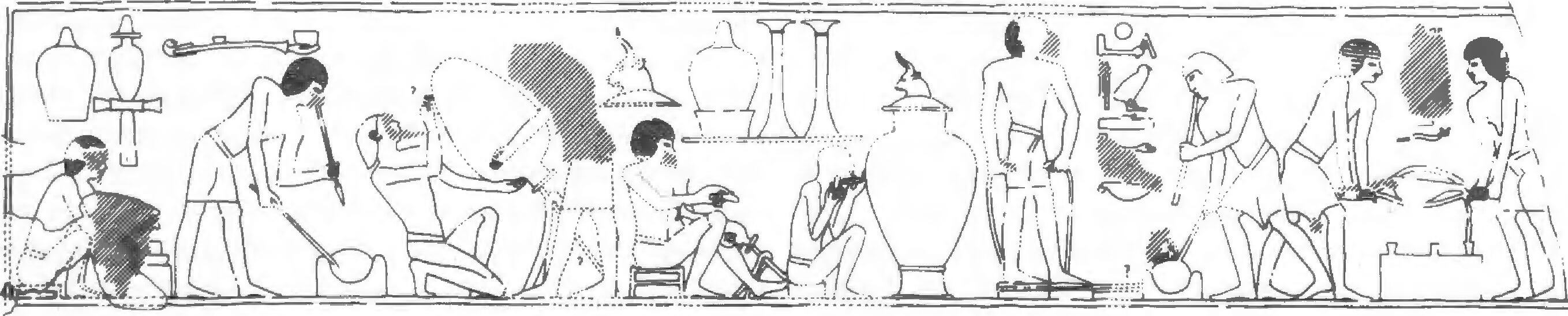
Page 156
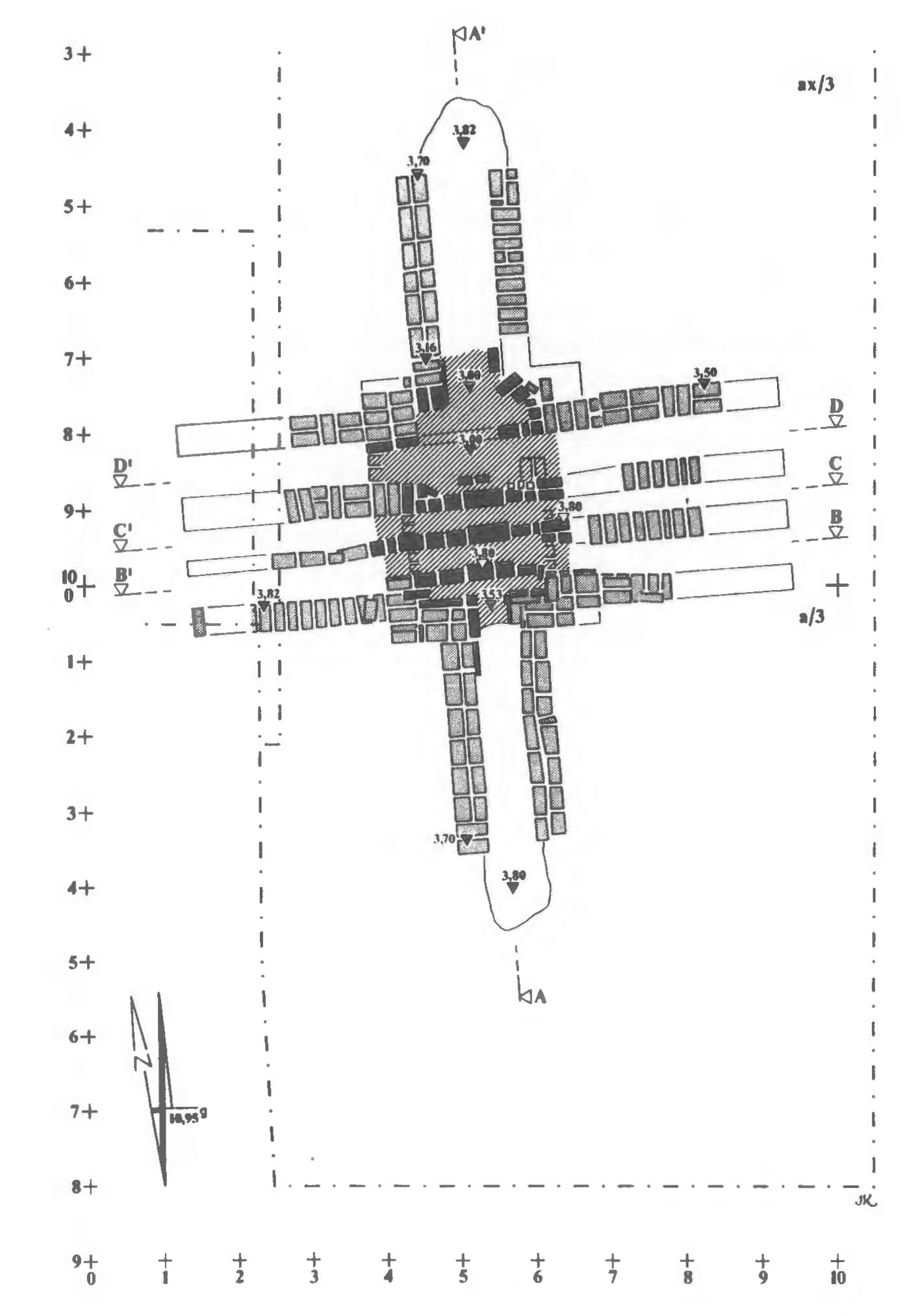
The best-known metal-working scenes are probably those on the wall of Rekhmira’s Eighteenth-Dynasty tomb at Thebes (Moo). These show various stages in the large scale production of copper alloy objects — from the arrival of the ingots to the casting of a temple door (Davies 1943; Wainwright 1944: 94-8; see Fig. 6.1).
The ubiquitous copper alloy statuettes representing a near-infinite selection of Egyptian deities are almost invariably from temple not funerary contexts. Enormous quantities of such statuettes have been found: Garland and Bannister (1927: 83), for instance, noted how the draining of the Lake at Karnak `provided almost a glut of certain varieties’,
and similar fortuitous finds have sometimes flooded the antiquity market since. A cache of more than ‘co copper alloy figurines was excavated at North Saqqara in 1968/9 (Emery 1970). Unfortunately, despite the quantity, quality and almost pristine condition of these pieces (many examples had been wrapped in linen), a proper study of technology, material or surface has never been carried out.
Such caches (paralleled in stone sculpture) do call into question any general policy of recycling ‘sacred’ copper-alloy objects. This would suggest that temple workshops required a steady source of newly mined raw material. After a review of Egyptian glaze compositions, Kaczmarczyk and
Page 157
Hedges stated that ‘The data . . . lead to one inescapable conclusion: from the sixteenth century BC onwards arsenical copper and tin bronzes were used on a regular basis as a source of copper in the faience industry.’ (Kaczmarczyk and Hedges 1983: 9o) and ‘from the Eighteenth Dynasty on bronze scrap was the primary source of tin in faience’ (1983: 239). In consideration of what has just been said, we might suggest that by-products of metallurgy, not recycled objects, might have provided much of the raw material for glaze, glass and pigment manufacture. If so, a close association of metal-working and faience/glass (and perhaps pigment) production must be assumed.
The simplest manufacturing process would be to hammer out small ingots, prills or even bits of native copper into sheets which could then be bent and cut into the required form. The skills needed to raise complex three-dimensional vessels from sheet and to join separate components by rivets and other mechanical methods had been acquired by the First Dynasty. Fine examples include a First-Dynasty find made at north Saqqara some sixty years ago (Emery 1939). Such techniques were usual for metal vessels throughout Dynastic times in Egypt. Vessels were seldom cast, the only common exception being the ubiquitous Late Period situlae with their relief decoration. If the monumental copper figure of Pepi I is of hammered, not cast components, (see p. 158) it would represent the pinnacle of surviving Old Kingdom sheet metal-work.
With the exception of most vessels and containers, and some simple implements, Egyptian copper alloy objects were generally cast to virtually their final form, whereafter only cleaning, and perhaps the addition of details, was needed. Cast weapons and tools however, did require serious mechanical working to harden and toughen the edges enough to be serviceable.
Some sheet-like objects, such as menits and mirrors, might have been largely formed by hammering, but the finer, more plastically modelled, openwork menits and the comparably worked vase-stands of the Eighteenth Dynasty were probably cast and might indicate the introduction of new casting technology.
The ability to generate the heat to smelt copper meant that the heat necessary to melt and thus cast copper was equally achievable. The main problem lay in generating the concerted heat need to melt and cast reasonable quantities of metal. Blowpipes, sometimes in banks, were used to maximise the heat for melting copper and other metals in the earliest times — they are represented at least as early as the Fifth Dynasty (Lucas 1962: 213, Scheel 1989). Pot bellows, in which a leather top on the flared opening of a pottery nozzle is pumped up and down by hand or foot to force a jet of air out of the narrow end, appear to occur first in the Middle Kingdom (Nibbi 1987; Davey 1979; Tylecote 1986). However, there is no representational evidence for such bellows prior to the Eighteenth Dynasty. It might be doubted whether larger masses of metal, such as that
needed in the initial stages of the manufacture of the Pepi I statue, could be obtained with simple blowpipe technology. However, it has recently been demonstrated that crucible smelting of copper, and thus melting of copper, is quite feasible with a bank of three to six blowpipes (Craddock 1995: 127). There is no evidence that large-scale casting was carried out away from the Nile in the mountainous mining regions where the prevailing winds could have been harnessed.
The simplest form of casting is to pour the molten metal into open moulds carved in stone, shaped in pottery or even formed in sand. More complex, three-dimensional forms required moulds made up of two, three or more sections that could be dismantled to remove the casting. However, at least some of the surviving moulds in terracotta and stone were probably used to make the ‘wax’ models for use in the lost-wax casting process, not to directly cast the final object.
Objects, such as ingots, flat axes and chisels were being cast by early Predynastic times. Lucas described the earliest Egyptian casting known to him as an axe-head of middle Predynastic date found by Brunton at Matmar which, according to the report by Carpenter, was cast and then hand-worked — either hot-worked or cold-worked plus annealing (Carpenter 1932: 625-6; Lucas 1962: 213). The composition of the axe head was almost pure copper with just minor impurities including 1.28 per cent nickel and o.15 per cent iron.
In the process of lost wax casting a model of the desired object is modelled or moulded in wax or some other material which is easy to model and has a low melting temperature. The use of beeswax per se should not be assumed. In more recent times, a resin/oil mixture or wax/resin has generally been employed and even lead has been used at some periods. Beeswax alone is often too soft particularly for complex or thin articles in warmer climates and today metal-casters can have separate recipes for summer and winter ‘waxes’.
The wax model is coated with the ‘investment’ material, usually clay with an organic binder like dung or chaff, and a hole pierced down from the outer surface to the model. When the clay is fired the wax burns or flows out and molten metal can be poured in. Once cooled and solidified, the mould is broken to extract the casting. The object then typically requires the removal of any surface protrusions or flaws (not the least being the sprue — the attached metal that has solidified in the funnel-shaped pouring hole). The piece is generally given final surface details and polished. A copper alloy statuette of Harpocrates still in its investment has been published (Williams 1919: 3-7).
In practice, certain refinements to the process were required. Air escape holes through the investment would facilitate the complete filling of the mould by metal, as would links between parts of a complex shape. Garland, for example illustrates the ‘runners’ linking the legs of an unfinished solid cast ibis (Garland and Bannister 1927: 45).
Page 158
Hollow castings are made by modelling the ‘wax’ around a central core. Hollow casting would not only save metal but, as Becker et al. (1994) have recently pointed out, it would also result in less potential shrinkage and thus less distortion in the mould. The interior core was perhaps most usually made from the same sandy clay/organic material as the investment. Such cores turn black on casting when the organic matter plus any absorbed waxes or resins burn. Blackened cores of this type are typical of Egyptian and other ancient hollow-cast copper alloy objects. There is potential for the dating of such cores by thermoluminescence techniques (Riederer 1978a). Other core materials include gypsum, (presumably plaster suggesting that such a material might also have been used for some investments), calcium carbonate in some form or other (conceivably carved limestone, see Riederer 1982: 30) and even wood (Schorsch 1988). Some cores inside animal figurines were intended to be removed after casting, in order to permit the insertion of a mummified animal (Jett et al. 1985).
Lost-wax casting was used for copper objects by the Old Kingdom. The use of casting for large-scale objects, such as the monumental statues of Pepi I and his son, remains unproven. Garland and Bannister (1927) suggested that the fine shaping and detail of Pepi (evident in the best photographs), together with the thickness of the metal, would make hammering a most unlikely option. Assembly of several separate castings would be the only option here, if indeed casting was used. Garland and Bannister did note the visible rivets as evidence for assembly from cast sections, but presumably hammered components would also require rivets.
Early lost-wax castings include the separately made and inserted spouts in some Old Kingdom ewers which date back at least as far as the Fourth Dynasty (Garland and Bannister 1927: 35; Lucas 1962: 215; Schorsch 1992). These, of course, are hollow and thus represent the initial stages towards the production of true hollow-cast objects (Nofal and Waly 1998).
Exceptionally fine figural hollow castings in copper-tin alloys had appeared by the Middle Kingdom — as witness the magnificent Fayum find which included the Louvre statuette mentioned above (p. 153) (Delange 1987: 211-13) and the statuettes now in the Ortiz collection (Ortiz 1994: cat. nos. 33-7). These magnificent hollow-cast statuettes show the ingenious multi-part assembly methods used even as early as the Middle Kingdom. The Louvre standing male figure has slotted-in arms and inserted lower legs and the large Ortiz figure of Amenemhat III (Ortiz 1994: cat. no. 36) has both a separate wig and arms held in place by vertical slotted grooves. This use of fine, thin-walled, hollow casting and mechanically inter-located sections shows a level of fine bronze-working skills hitherto not expected prior to the Ramesside or Third Intermediate Period. Here, as with many of the finer castings, it is difficult to gauge the
extent of hand-working. The large female consort from the same group, and also in the Ortiz collection (Ortiz 1994: cat. no. 35), is just as finely hollow-cast with a core still in place (the walls of the arms being only around four millimetres thick).
Most copper alloy statuettes of the Second Intermediate Period and the early New Kingdom appear to be solid cast. Datable examples include one of the Second Intermediate Period, now in Brooklyn, depicting a squatting, nursing mother, her uraeus and the inscription identifying the group as a royal princess and her son. This is a consummate one-piece, solid casting, perhaps a copper-tin alloy, with plenty of negative space and with post-casting hand worked detail and inscription (Brooklyn 43.137).
The dearth of early and mid-New Kingdom copper alloy figures, either solid or hollow cast, is quite remarkable (Vassilika 1997). It is noteworthy that the majority of the surviving examples are royal — although, of course, these are the most dateable category and other non-royal examples might well reside in collections with later ascribed dates. The examples include a fine, solid-cast kneeling figure of Thutmose III in black bronze (see p. 16o) with gold inlays, which has recently been acquired by the Metropolitan Museum of Art, New York (1995.21; see Hill 1995) and the British Museum statuette of Thutmose IV (BM EA64564) which also appears to be solid-cast. As with the New York piece, the arms are separate and located over square dowels projecting horizontally from the shoulders. There is also careful post-casting hand work.
Fine hollow castings, on the basis of the scanty evidence, appeared again at the end of the Eighteenth Dynasty as witnessed by a black bronze kneeling figure of Tutankhamun now in the museum of the University of Pennsylvania, Philadelphia (Fishman and Fleming 198o). In the Ramesside period, copper alloy sculpture began to become slightly more common. Three fine examples can be seen in the Metropolitan Museum of Art, New York. One is, again, a kneeling figure, perhaps solid-cast, this time of a man wearing characteristic Nineteenth-Dynasty garb (Hayes 1959: 382). The others are a standing figure of a shaven-headed priest and a late New Kingdom, hollow-cast small head with inlaid eyes (Hayes 1959: 381-3) A fragmentary, rather thick-walled, hollow-cast figure illustrated by Garland bears the cartouche of Rameses IV (Garland and Bannister 1927: 47-8).
As noted, complex objects were typically made up from separate components — sometimes part cast, part wrought — and generally joined by mechanical methods. Of these mechanical techniques, the simplest example are rivets as typically used for such purposes as attaching vessel and mirror handles.
The most common ancient joins on figurines are those connecting the arms to the trunk and, as might be expected, the types of join employed tend to mirror those found in woodwork (see Chapter 15, this volume). The simplest are
Page 159
just pegs or dowels, but there are also many variations on the tenon and mortise joint, often with wedge-shaped slots. Just when wedge-shaped rather than straight pegs or tenons were developed remains uncertain. A fine Middle Kingdom male figure in the Louvre has straight tenon shoulder joints (Delange 1987: 211-13), as have the Ortiz kneeling figures of Amenemhat III and his consort (Ortiz 1994: cat. nos. 35 and 37). Once assembled, joint lines could be disguised by hammering or burnishing or concealed by chased details such as arm bands and shoulder straps.
In the Late Period, one-piece castings were more often used, again. In part this was a result of the typically simpler, often cruder, forms, but it was also true that the fluidity of the now popular heavily leaded alloys permitted more complex shapes to be cast in one. When separate components were required — these were most often arms — one or both being made separately and added, depending on size and pose. An over-life-size head of a pharaoh now in Hildesheim was formerly identified as a Rames side ruler but is in reality almost certainly a Twenty-ninth- or Thirtieth-Dynasty piece and a rare example of near-monumental hollow casting (Eggebrecht 1993: 90—I).
Soldering or braising was very seldom used on copper alloy objects in Egypt during Dynastic times and perhaps never for attaching the various components of statuettes. The use of a silver solder for copper has been reported for joining sheet copper as early as the Fourth Dynasty, when this technique was used for the copper sockets of Hetepheres’ canopy supports (Lucas 1962: 216). The seam of a copper (or bronze) trumpet from the tomb of Tutankhamun is similarly assembled (Lucas 1962: 216) and the technique is sporadically reported for other times and places in the ancient world (Ogden 1983a: 67). Both silver and lead were used to plug working defects in an Eighteenth-Dynasty cow vessel — a category of object that represents the rare use of casting for New Kingdom figural objects (Win-lock 1936: 147-56). The presence of solder on Egyptian copper-alloy statuettes is usually indicative of recent repair or forgery. Casting-on was sometimes used (see below) and the recent report of the feet of a Third Intermediate Period female statuette being ‘welded’ on might, rather, be an example of this (Raven 1992).
Roeder noted that the wax models used to cast the ubiquitous Egyptian copper alloy statuettes, both solid and hollow, could be made up from separately formed wax components — torsos, limbs, heads and so on. This would be the natural approach when the figures were being entirely hand-modelled — only the simplest forms could be created from a single initial block of wax. The improvements in precision and the possibilities of mass production permitted by moulding or casting the wax components would be a natural next step and the use of plaster moulds to produce a series of identical components (or occasionally complete figures) is probable. Recent study of copper alloy figurines in Leiden appears to confirm the use of
pre- moulded wax parts in just this way (Raven 1992).
The Leiden project has also identified another casting process which is well-substantiated in antiquity in general but seldom reported from Egypt (Garland and Bannister 1927: 69; Raven 1992). This is ‘casting on’, a process by which a deficient or missing area of a cast is moulded in wax onto the existing metal object and then the whole area coated with the investment and new metal cast in. The apparent presence of the technique on several objects in the Leiden collection suggests that the procedure might have been relatively common. Another Egyptian example is the cast-on base (to a raised vessel) recently described by Schorsch (1992: 141-59). Care must be taken in identification. It can be difficult to differentiate between casting-on and areas where two wax components of the original casting antetype were joined, perhaps with crudely added or smeared-over wax. Metallographic study of a section taken from the area is the best guide, but for obvious reasons seldom resorted to.
Support for the cores during the production of hollow castings also needed consideration. Supports were not required when hollow castings had openings (e.g. on the underside of the bodies or at joins in multi-part objects), because the core would have been in direct contact with, and thus held in place by, the surrounding investment.
Holes cut in the wax would create contact points between core and investment and provide the necessary support. This might explain the mysterious so-called ‘dowel holes’ both in the Philadelphia figure of Tutankhamun mentioned above (p. 158) (Fishman and Fleming 1980) and in a figure of Min-Amun in the Fitzwilliam Museum, (E49b, 1954 Vassilika 1997), and although this cannot be proved in Egypt, such a technique was later used by Greek metal-casters (Haynes 1992: 70-1). The holes left in the final casting could be plugged or concealed under gesso and gilding.
Late Period copper alloy castings sometimes retain traces of iron wires ‘chaplets’ used to hold the cores in place (Garland and Bannister 1927: 39-41; Schorsch 1988). Schorsch (1988) has recently pointed out that fakes of Egyptian bronzes often have far more core supports than their ancient counterparts. The recent study of a fine large Third Intermediate Period hollow-cast female figurine in Leiden revealed, rather surprisingly, an internal iron rod support which passed through the trunk and divided down each leg to the heel (Raven 1992). The use of iron wire supports in New Kingdom copper alloy objects is unlikely, but we can note that Renaissance practice as well as recent forgeries of Egyptian copper alloy statuettes demonstrate that relatively pure copper struts can be employed to hold cores in place in leaded copper alloys.
Care had to be taken in all stages of casting and finishing. The fine, thin-walled hollow castings of the Third Intermediate Period and, less so, of the Late Period, were prone to core expansion and cracking at the time of manufacture if the core retained any moisture. As Garland noted, this
Page 160
means that not all cracks and distortion in such objects can be attributed to post-burial corrosion (Garland and Bannister 1927: 43). Hand-finishing of solid castings was quite practical if required. However, the fine, hollow-walled ones, perhaps most typically of Third Intermediate Period date, would be prone to damage by any serious mechanical working and there would have been sense in including as much of the fine detail as possible on the original wax model. The chased detailing of copper objects and the accurate cutting or sharpening up of inlay recesses would be an obvious use of iron tools, but the fine Middle Kingdom copper alloy statuettes show that iron tools were not mandatory.
The quality of workmanship of the.Third Intermediate Period figures is, on average, far better than those of the Late Period when, we must assume, the rapid expansion of the industry led to much mass production of poor-quality goods being produced for temple offerings. What this says about changes in Egyptian religious practice at a time of foreign rule is outside the scope of this chapter.
Decorative inlays and overlays on copper alloy objects
The overlaying of all or part of a copper alloy object with gold, electrum or silver sheet is well-known from ancient Egypt. In the simplest technique the precious metal sheet is pressed and shaped over the object and held in place by adhesive, mechanical folds or overlaps. The commonest technique, probably from the late New Kingdom onwards, was to gild with extremely thin gold leaf laid over a thin layer of gesso. To facilitate the adhesion of the gesso to the copper alloy, the object was sometimes roughened by stippling or chiselling (Garland and Bannister 1927:191; Oddy et al. 1988) or by glueing linen to the metal and then applying the gesso over this.
The gold leaf can be extremely thin — down to under 0.005 millimetres (Lucas 1962: 231). The present writer has seen cases where the gold leaf is thin enough to appear greenish by transmitted light. The nature of the adhesives used have not been ascertained but were presumably ordinary animal glues or albumen (see Chapter 19, this volume). In one unpublished Late Period example examined by the writer, minute particles of bird’s feather were identified in the glue holding gold leaf to a lead substrate. This might represent the use of feather brushes — a suitable application implement as attested in medieval literature.
It has often been assumed that the even, black colour now seen on some Egyptian copper alloy objects, in particular inlaid examples, was deliberate (Ogden 1983a: caption to fig. 4.1; Craddock and Giumlia-Mair 1993). Recent research has shown that the effect, which is essentially the same as the more recent shakudo work from Japan, is due to the addition of a few per cent gold, often containing a little silver, to the alloy. After stringent cleaning and polishing, probably with a vegetable extract or juice as per the Japanese technique, the object is treated with an acid solution made from such ingredients as copper sulphate, alum and nitre.
This results in a fine, compact and durable bluey-black copper oxide layer. This surface coloration makes an ideal background for inlay work in gold, silver (or electrum) and even copper, and, indeed, this is its most usual function.
The use of this technique in the ancient Old World was first noted on Roman objects. However, observation and analysis soon established its use on earlier Classical pieces — such as for the black inlaid strips decorating the finest Mycenaean dagger blades (Ogden 1993) — and then on Egyptian objects from the Middle Kingdom through to the Late Period (Ogden 1993; Craddock and Giumlia-Mair 1993; Craddock 1994;1995b; Giumlia-Mair 1996). Middle Kingdom examples of ‘black bronze’ include the kneeling figure of Amenemhat III in the Ortiz collection (Ogden 1994; Giumlia-Mair 1996), a crocodile from the same group now in Munich (Giumlia-Mair 1996), and also a scimitar blade in Munich (Giumlia-Mair 1996). This latter has a copper alloy blade with a narrow band of black down each side inlaid with inscriptions and designs in gold wire —thus relating it closely to the well-known Mycenaean blades. In the New Kingdom we have the kneeling figures of Thutmose III and Tutankhamum noted above (p. 158). Once into the Third Intermediate Period and Late Period, examples became more plentiful.
Black bronzes tend to have up to about 5 per cent gold and, typically low lead levels, even in the Late Period. Black bronze has been equated with the hymn-km (black copper) referred to in Egyptian inscriptions from the early Eighteenth Dynasty onwards (Giumlia-Mair 1996; Craddock 1998). The recent research on what are probably surviving examples of hsmn-km vindicates the view of Garland and Bannister three-quarters of a century ago. They noted that the supposed blue colour of some ancient bronzes ‘must necessarily have been in great measure due to the composition of the bronze itself, not improbably containing gold’ (Garland and Bannister 1927: 82).
Black bronzes are probably just one example of an ancient tradition of deliberately colouring or altering the surface of ancient metals. For example, the New Kingdom cow vessel in the Metropolitan Museum of Art, New York, mentioned above, has a surface which suggests deliberate chemical etching of some type prior to the attachment of the cow figure (Winlock 1936).
As noted below (p. 164), pigment has been observed on some gold and probably silver objects from Egypt and, as seen with copper—tin and copper—arsenic alloys (p. 152-3), some link between alloy and intended colour sometimes seems inescapable. However, the idea that the blackish inlay on the cheek of a Horns falcon deity in the British Museum might be due to deliberate treatment with an arsenic compound (Shearman 1988) has now been rejected (see Craddock and Giumlia-Mair 1993).
A Late Period cast copper alloy situla in the Metropolitan has an unusual surface layer of a high lead copper alloy. This appears to have been applied by dipping the situla into
Page 161
a molten lead-copper alloy and was ‘subsequently re-chased and polished to simulate silver’ (Young 1959). The present writer has noted what appears to be a similar technique on an Archaic Greek figure. Plating silver by dipping in an electrum alloy is referred to below (p. 165).
Gold and electrum
Bright yellow gold needs no introduction. Admired and desired for millennia, it was available as a native metal and required no complex or laborious smelting procedures. Perhaps the greatest puzzles are why its employment does not appear to precede that of copper or lead or why it has never been reported from a Palaeolithic occupation site.
Gold, formed deep within the earth’s crust, is forced up through fissures in rocks to form veins, usually in quartzites. This vein or reef gold can be mined, but it is arduous work to break and grind up the rocks to release the particles of gold. However, nature lends a hand and over long periods of time wind, rain and frost break up the gold-bearing rocks and the grains and nuggets of gold are washed down into the streams and rivers where they congregate as alluvial or placer gold. Over further geological timespans some of this gold is incorporated into new rock formations.
The mines
The gold-mining regions in, or adjacent to, Egypt essentially stretch southwards through the Eastern Desert from roughly the level of Qena-Quseir to as far down as the present Sudan border, although there are some sources, exploited in antiquity, further north in the Eastern Desert. Since the gold mines of ancient Egypt were celebrated in Classical and in Medieval Islamic times, many travellers to Egypt in recent centuries have explored the mining areas. There was some mining of Egyptian gold in the twentieth century, with a reported production of almost seven tonnes between 1902 and 1958 (Sabet et at. 1976a). In recent times further geological surveys have been made, some aided by satellite photographs, and the renewed exploitation of Egyptian gold is still under consideration.
Documentary evidence shows that the Egyptians themselves defined three gold mining regions (Vercoutter 1959). The gold from mines in the Eastern Desert in the Hammamat to Abbad region was referred to as ‘gold of Koptos’. Koptos was an important trading centre on the Nile which controlled much of the Eastern Desert produce. Further south, ‘gold of Wawat’ was obtained via the Wadis Allaqi and Gabgaba. The caravan routes started on the Nile at the fortress of Quban, a settlement that might have owed its foundation to the need to protect these routes and which was also, perhaps a processing centre for other produce of the area — such as copper ore (see p. 151). From still further south, from what is now the Sudan, even parts of Ethiopia, came the ‘gold of Kush’.
Surveys undertaken between 1989 and 1993 by a corn-bined Egyptian Geological Survey and Munich University team studied around 13o ancient gold mining sites in the Eastern Desert over an area roughly between the twenty-second and twenty-eighth parallels (Klemm and Klemm 1994). This research revealed extensive mining activity in the Eastern Desert from Predynastic time onwards and showed how the types of gold deposit exploited changed with time as recovery techniques improved.
In Predynastic and Early Dynastic times exploitation was fairly sparse, but spread over much of the Eastern Desert right down to the region between Aswan and Ras Banas. The Castiglioni brothers have reported the possibility of a Neolithic settlement at the gold-mining centre of Deraheib in the Wadi Allaqi (unpublished). This settlement was a major city in post-Pharaonic times and most of the buildings and mining detritus are late in date, but there is also Middle Kingdom and pan-grave pottery.
There is little in situ evidence for the direct exploitation of anything other than Koptos gold in the Old and Middle Kingdoms. However, the surviving documentary evidence indicates that the gold of Wawat, if not Kush, played a vital part in the Middle Kingdom and up to the middle to late New Kingdom. Examples of such textual evidence include several Middle Kingdom stelae, such as two in the British Museum: that of Simunt, discussed below (p. 162), and that of Sa Hathor. The latter, dating to the reign of Amenemhat II, explains how Sa Hathor went to the south to supervise the gold-mining and gold-washing.
This exploration for southerly gold sources might suggest that the more northerly Eastern Desert mines had been largely exhausted (within the capabilities of primitive mining technology) by the early days of the New Kingdom. Whether newly developed mining technologies made the Eastern Desert mines more economic again in the later New Kingdom, or whether changing political situations to the south made necessary a re-think about Eastern Desert exploitation, is uncertain, but certainly the exploitation of Kush gold subsided until Napatan times. In the late New Kingdom, the focus seems to have switched back to the Eastern Desert. The famous map of the gold mines now in the Museo Egizio, Turin (Cat. 1879), one of the oldest surviving maps in the world, dates from the Twentieth Dynasty, and might reflect a resurgence of interest in the Koptos gold at this period.
There is still much work to be done collating the geological, archaeological and documentary evidence regarding the exploitation of the various gold mines within reach of Egypt, but Greaves and Little’s succinct words from 1929, quoted by Lucas, still apply: ‘No workable deposits [of gold] have been discovered that they [the ancient Egyptians] overlooked’ (Greaves and Little 1929: 123-7).
The gold grains and nuggets in a river bed, or in what had once been a river bed, can be recovered relatively simply. Initially hand-picking probably sufficed, but a more productive approach was panning in which the sands and
Page 162
fine gravels of the river bed are scooped up with water in a pan-like vessel and swirled around. The sand and water slosh out over the sides to leave the far heavier gold particles in the bottom of the pan. For larger-scale operations, the sand and water are run down over a sloping washing table which has suitable grooves, ridges or other arrangements to trap the gold grains. This process is called gold-washing and is also used in the recovery of vein gold once the gold-bearing rocks have been broken up and laboriously ground down to powder. Ancient gold-washing tables have been reported and illustrated by Vercoutter (1959)
Although we see representations of gold-workers in tomb decoration from the Old Kingdom onwards, the earliest representation of gold recovery is that in the tomb of Baqt III at Beni Hassan (BH15) which dates to c. 1900 BC. Here we see gold ore being sorted or washed, perhaps ground, while a vertical object is possibly some type of gravity washing table depicted in plan view (Chappaz 1983). More recently the newly excavated tomb of Khacy, described as `goldwasher of the treasury of Pharaoh’, at Saqqara has revealed a scene of gold-washing with what appears to be grinding (?), a sloping washing-table, and melting. This tomb dates to the time of Rameses II (Martin 1991: 131 fig. 90; see also Fig. 6.4).
Grinding stones, perhaps predominantly of Ptolemaic and Roman times, can be seen in abundance in the gold mining areas of the Eastern Desert. The backbreaking work and the division of labour depending on age and gender at Ptolemaic gold mines was graphically described by Agatharchides as recorded by Diodorus Siculus (Oldfather 1935:121). We know that in Ptolemaic and Roman times the workforce was made up of prisoners of war, slaves and convicts. Although the descriptions of the mine workings from the Dynastic period are far less explicit, the mental images generated by Agatharchides comes to mind when we read, for example, the Twelfth-Dynasty stele of Simunt in the British Museum (BM EA828). This tells us how he went to the south to bring back gold for Amenemhat II and how he made men, women and children dig out the quartz then crush and wash it. This stele does raise the question of
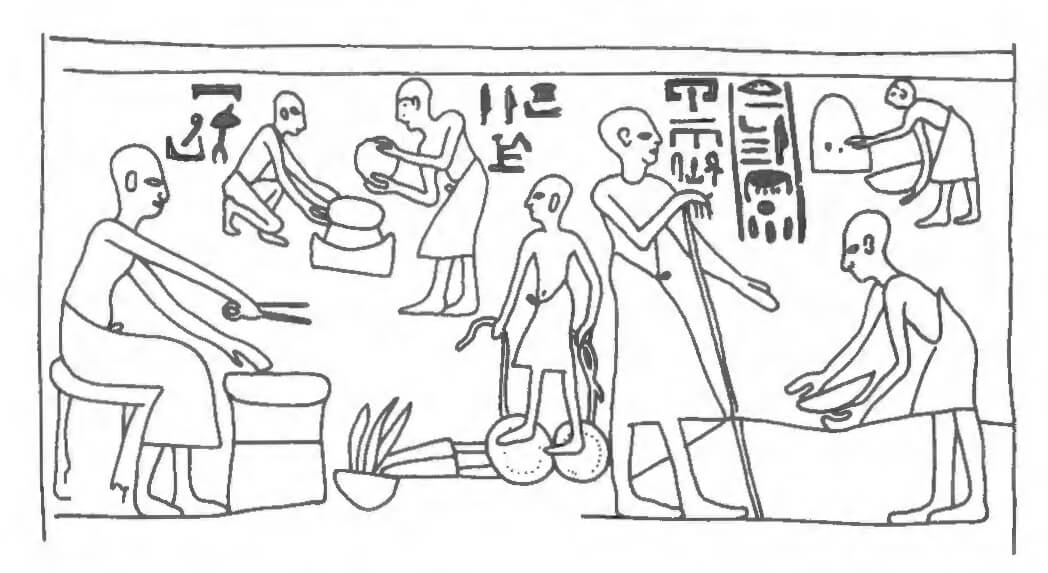
the extent to which vein gold, as opposed to the easier-toexploit alluvial gold, was exploited in Dynastic times. There seems to be little evidence for the mining of vein gold prior to the Middle Kingdom and alluvial gold was still probably a major source in the New Kingdom and even later.
Once mined, the gold would have been transported to the centres where it was to be worked. For security and ease of recording, the gold would have been melted into ingots of some type, unless it was present as relatively large nuggets. We see the transport of both nuggets and ring ingots in New Kingdom wall paintings, and gold has been transported in identical forms in recent times in Ethiopia.
Some import of gold from outside Egypt, as tribute or booty, is probably likely to have occurred on a fairly minor scale throughout Egyptian history. We only have documentary evidence for imports of gold ‘from the North’ from the Ramesside period onwards, but tangible earlier examples might indude the ten gold ingots found with the predominantly silver ‘el-Tod treasure’ of the Middle Kingdom (de la Roque et a1.1953). This possibly originated in Anatolia (see under ‘silver’ p. 170.
Composition and refining
Gold, as recovered from the earth (native gold), can vary greatly in composition. The predominant accompanying element is silver, which can be homogeneously alloyed with the gold in anything from mere traces up to 5o per cent or more. The copper content of ‘as-mined’ gold is typically under about 2 per cent, but there are exceptions, and there will generally be detectable traces of numerous other metals including iron, tin and members of the platinum family of metals.
The nature and relative proportions of the trace elements in gold potentially provide an indication of source or source type, but so far there are too few analyses of gold objects or mine samples and, besides, there can be considerable variation in the composition of native gold even within the same mining area, particularly with alluvial gold. Osman (1995: 8) has recently noted that the gold is more pure in the southerly regions exploited by the Egyptians than in the north. More precise characterisation of Egyptian gold sources might be possible in the future. For example, the presence of antimony ores in association with gold has been noted in the Eastern Desert at Wadi Ballit and Fawakhir (Hume 1937 and Azer 1966), and so we might suggest this area as a source for the gold used for the sceptre of the Second-Dynasty pharaoh Khasekhemwy with its celebrated, and previously puzzling, small antimony content (Lucas 1962: 226-7; Ogden 1976).
Traditionally gold with over 75 per cent gold present is described as gold. If it is a gold—silver alloy with under 75 per cent gold it is electrum, and, according to Gale and Stos-Gale’s more recent nomenclature (1981), gold—silver alloys with 5 to 5o per cent gold should be termed aurian silver (those with less than 5 per cent gold are simply
Page 163
termed silver with low gold — see section on silver, pp. 170-171). Although a simple terminology for mined gold, this is, perhaps, not a good reflection on how the alloys were considered by the Egyptians, or behaved when they worked them or buried them. The traditional division between electrum and gold at 75 per cent gold level falls most inconveniently at just about the median composition for much Egyptian gold-work. Also the variable copper presence will have a major effect on colour and the effects of burial (or even deliberate post-manufacture surface treatment) can greatly ‘improve’ the surface colour and thus apparent purity (Ogden 1983b,1993).
The possibility of distinguishing between natural and man-made gold—silver alloys has been raised from time to time (Weill 1951). A small lead content is usually taken to be indicative of man-made alloys, that is gold alloyed with smelted silver, but this is perhaps not an invariable rule (Ogden 1993: 39).
Iron is found in trace levels in much ancient gold. Tin, which is potentially perhaps a better indicator of source, is quite common in Egyptian gold objects (perhaps most typically in the New Kingdom, but far more analyses are needed). The tin is generally homogeneously distributed in the gold in solution, but the author has also noted what appear to be very minute inclusions of some type of hard tin mineral in Ptolemaic gold objects, and the same might well turn up in earlier Egyptian gold. Silvery-grey inclusions of the platinum-group metals are also extremely common in gold objects from Egypt (see pp. 169-70).
The composition of an ancient gold object can reflect four possible practices:
- Gold can be used ‘as found’.
- Gold can have silver, copper, sometimes both and occasionally other metals, alloyed with it for aesthetic, practical or even fraudulent reasons.
- Gold can be purified (refined) and employed in a pure or near-pure state.
- Gold can be refined and then alloyed down to the desired fineness level by careful measured additions of silver, copper or other metals.
These four possibilities also represent the chronological development of gold usage. One might expect the use of gold in as-mined (or as-recycled) state to have been the norm for much of Egyptian history. However, analyses of gold objects from Predynastic times onwards show that copper is often present at levels far above those of natural impurity and a deliberate addition seems certain — a feature, also, of some contemporary Sumerian goldwork. The addition of considerable amounts of copper to produce a deliberate red colour is seemingly an Amarna-period phenomenon, as noted below (p. 164). Nevertherless, as a rule of thumb, copper levels in gold were nearly always lower than the silver levels — a fact true for most of the ancient world up to, and including, Roman and Byzantine times.
The ancient Egyptians had no way of accurately assessing the composition of gold as mined and nor would they have been able to predict or determine the eventual composition of gold deliberately alloyed with other metals. This means that standardisation and accurate assessment of value (and, outside Egypt, the possibility of developing sensible coinage) were well-nigh impossible before mined gold could be `refined’ to bring it to a pure state. Once refined gold was a reality, carefully weighed proportions of other metals could be added to provide predefined gold alloys.
The date of the introduction of gold refining is a much-debated subject. Chappaz (1983) has pointed out that in representations of metal-workers melting gold with either blowpipes or foot-bellows, we often also see one workman blowing air into the crucible with a blowpipe. For example, in the New Kingdom tomb of Puyemra at Thebes (TT39), gold is being melted with one man operating a pair of foot-bellows (see Fig. 6.2). However, a second man appears to be stirring the crucible with one hand while blowing through a blowpipe into the crucible. This would certainly help to oxidise any base metals present, particularly if extra lead or lead oxide was added (true cupellation). However, there would be no significant loss of silver and thus little if any overall increase in purity of typical as-mined Egyptian gold. This means that the oft-published Amarna letter that refers to the drop in weight when the Egyptian gold was put through Mesopotamian fires must be assumed to refer to a more efficient silver-removing refining process (EA 1o; Moran 1992: 19-2o), unless a batch of the gold—copper alloys typical of the Amarna period (see p. 164) had been sent overseas (Ogden 1993).
Despite this Amarna letter, the available analytical evidence suggests that refining was not used in the day-to-day jewellery industry before the Late Period, and was perhaps introduced by the Persians. The same chronology would also appear true for much of the ancient Near East and the Classical lands, and relates to the introduction of standardised coinage in Asia Minor at about that time.
On the basis of published analyses (as well as the writer’s own largely unpublished analyses), it appears that Egyptian gold objects prior to the Late Period were generally unrefined and probaby simply gold as-mined (or otherwise obtained) with some addition of copper in some cases. This copper — presumably intentional — can range up to io per cent, with the copper levels at the upper end of this range perhaps being more typical after the middle New Kingdom. In view of the beneficial effects of copper in improving the `gold’ colour of gold—silver alloys, as noted above, it might not be coincidence if there was an increase in copper levels from a time when ‘gold-coloured’ gold was beginning to be valued more than the paler electrum alloys.
Ancient Egyptian gold purities can thus range from well under 5o per cent up to 90 per cent or more. Purities over about 85 per cent appear to be rare before the Late Period, and around 7o per cent to 85 per cent seem most typical of
Page 164
jewellery of the Middle and New Kingdoms. Berthelot (1895) notes that two examples of the gold from the Twelfth-Dynasty `Dahshur Treasure’ were around 83-6 per cent gold, the balance being silver. Copper was less than per cent.
Nevertheless, some alloys are far less pure and some gold objects, perhaps often of natural alloys, have silver levels exceeding the gold (e.g. the aurian silver examples published by Gale and Stos-Gale in 1981). Other examples include a Middle Kingdom shell pendant in the Fitzwilliam Museum (E.3o2a, 1947) which has just over 3o per cent gold, about 66 per cent silver and around 3 per cent copper, and a similarly low level of purity was noted for some gold foil from the Twelfth-Dynasty burial of Senebtisi (unnumbered fragments; Frantz and Schorsch 199o). There was a similarly large range of compositions in the New Kingdom although, perhaps, a trend to higher average purities. There are few analyses available of Third Intermediate Period gold, but the evidence suggests much the same pattern as in the New Kingdom — including some low purities. For example a Third Intermediate Period vertical amulet case in the Fitzwilliam Museum has only about 5o per cent gold (E12.194o; see Ray 1972, unpublished analyses by Ogden).
Gold purifies over 90 per cent, and often around 95 per cent, only become common in the Late Period when, as suggested above, refining perhaps began to be used on a more regular basis. For gold leaf (for use in gilding) there was an advantage in high purifies — the higher the purity, the easier it is to produce thin leaves. More than 95 per cent purity seems fairly typical of later gold foils, such as on gilded Late Period copper-alloy objects. However, samples of gold leaf from Middle Kingdom wooden coffins ranged in purity from around 85 per cent or so gold right down to about 3o per cent gold (Frantz and Schorsch 199o). The recent analysis of the gold leaf on a silver plaque from the tomb of Nefertari showed it to be of high purity (99.o per cent) gold (Markowitz et cti. 1997). This might indicate the occasional use of refining in the Ramesside period — or if not, at least the deliberate choice of high purity gold ‘for hammering into thin leaf. A small gold plaque from the same tomb was composed of 81.7 per cent gold (Markowitz et al. 1997). High purity gold has sometimes been employed for the ubiquitous fakes of Egyptian gold objects, some dating back to well before World War I; some authorities in the past have even erroneously assumed that high purity was a positive sign of antiquity.
The addition of copper, as noted, counteracts the paling effect of silver on gold and if, as usually supposed, electrum (and silver) were considered more desirable than gold prior to the New Kingdom, the early addition of copper to electrum seems counterproductive. After the New Kingdom copper might have been intentionally used to ‘correct’ the pale colour of as-mined gold—silver alloys. The high copper `red golds’ used for some of the gold stirrup-rings of the Amarna and immediate post-Amarna Period (and perhaps
only for rings) are of some interest in studies of cultural relationships. There is enough copper — well over 5o per cent in some cases (Lucas 1962: 229; Ogden 1977) — to produce a strong red colour. Copper—gold alloys were used for deliberate, decorative purposes by the Mycenaeans at about the same period (Ogden 1993) and, interestingly, the Egyptian rings are, as a type, almost as well-known from Cyprus as Egypt. Alloying copper to gold reduces its melting temperature and makes it easier to cast. This might seem to be one explanation for these solid, and often massive, red-gold rings; the purer examples are seldom cast.
The highest copper contents in gold known to the writer from post-New Kingdom objects are in thin gold inlays in copper alloy objects and some diffusion of copper from the underlying metal might be assumed. Higher copper levels are also to be found in some gold solder alloys employed on gold objects — sometimes over 20 per cent copper.
The use of induced colours on Egyptian metals — such as the ‘black bronzes’ discussed above (p. 16 o) — is also seen in the bright blood or burgundy-red colour gold surface which was produced by small iron additions to gold. The process was discussed in depth by Lucas, who provided a bibliography of earlier work (Lucas 1962: 233-4), and it has recently been examined and replicated by Frantz and Schorsch (1990). The bright colour is only a thin surface layer and thus was not suitable for many items intended for wear. The best-known earliest examples are the beads, rosettes and ‘sequins’ from the tomb of Tutankhamun. The earliest instance recorded to date is from the Eighteenth-Dynasty tomb of Queen Tiye and the latest the Twentieth-Dynasty earrings of Rameses XI. The technique has so far only been encountered among royal funerary equipment.
The application of gold over copper alloys was noted briefly above (p. 16o). Various plating techniques were used but all involved the application of sheet-gold as foil or leaf. The use of ‘fire gilding’, using mercury—gold amalgams, was unknown prior to the Ptolemaic period.
In the simplest forms, sheet gold (ranging in thickness from the extraordinarily thin to the quite substantial) could be attached to the surface of other metals and such materials as ivory and wood (see Chapters 13 and 15, this volume). Thickish gold foil could be held in place by folding or crimping it over the edges of the object or into channels deliberately formed in the object. In some cases small nails or pegs were used. For thinner foils and gold leafthe easiest procedure was to glue it to the substrate — either directly to the surface or over an intermediate gesso layer (Ogden 1983a: 8o).
It seems unlikely that gold foil or leaf could be attached to copper alloys by a process involving heat and burnishing, since the copper alloys too easily develop surface oxides that would hinder adhesion, but such techniques were used to apply gold to silver in ancient times. Objects were sometimes made by fusing, by heat and hammering, gold over an electrum substrate and then hammering this out into a
Page 165
composite sheet from which objects could be formed (Ogden 1983a: 80—i). This technique was employed for some of the hollow annular ‘hair-rings’ of the New Kingdom. In one case examined by the writer, the surface layer was electrum with only a marginally higher gold level than the electrum underlying it. It seems economic nonsense to go to so much trouble to plate electrum with electrum, but an explanation might be that the surface layer was just sufficiently higher in gold to permit surface enriching (i.e. to be given a purer gold surface by chemical leaching). This technique, using various mixtures of alum, urine and other substances, has been employed until recent times. The generally accepted rule of thumb is that gold alloys with under about 55 per cent gold cannot be surface ‘coloured’ in this way.
The plating of silver by dipping into molten electrum, followed by chasing, was possibly used for some small amulet-like statuettes. Oddy et al. (1978) described a figure of the god Khons treated in this way, and the same technique appears to hai7e been used on a similar figurine recently examined by the present writer. The use of dip-plating to provide a silver-like lead—copper alloy surface to a copper alloy situla was mentioned above (p. 16o). This technique might be most typical of the Late Period, but so far few examples have been discussed.
Gold-working
The methods employed by the ancient Egyptian goldsmiths have been covered in some detail elsewhere (Aldred 1971; Ogden 1983a, 1992a), although there is still a need for a far more comprehensive study. As with copper alloys, all but the most primitive of gold objects would have passed through at least one melting state during their production history. Gold grains, dust or nuggets would be cast together into bars or rings for ease of transport and recording, and every time that gold was alloyed it would be melted with other metals. Early representations, such as that in the tomb of Mereruka at Saqqara (c. 2300 BC) show whole banks of workmen with blowpipes melting gold.
Nevertheless, the gold-working tradition of Egypt and the Near East was predominantly one of sheet gold, not casting. Objects were made by hammering out the gold —whether supplied as ingots, fused scrap or, later, coins —into thin sheet, which was then cut and shaped to form the individual components of the jewellery. Even components such as wires and small gold spheres were formed from sheet, the former by various cuffing, hammering or twisting operations, the latter by melting small snips of sheet or wire so that surface tension would roll them up into small balls. Even the more massive, solid objects, including some fine, gold amulets were generally made by hand-working gold, not casting.
When casting was employed for gold, it was often in conjunction with hand-wrought work. For example, a gold deity figure might be cast by the lost wax process, but it
might also have other components such as a rectangular sheet-gold base, attributes, hammered suspension loop and so on soldered in place. The problem was that casting was potentially wasteful of metal. There was no way to produce a mould or a wax antetype which would employ a pre-determined volume or weight of metal and every cast would have casting fins, sprues and so on which would have to be cut off.
Solid-cast gold objects, like their copper—alloy counterparts, could be made up from several separately cast components. For example the fine Twenty-second-Dynasty gold figure of Amun in the Metropolitan Museum of Art, New York (MMA 26.7.1412) was cast, with fine surface working, but the arms appear to have been made separately (by casting?) and soldered in place. The headdress plumes and base plate are of sheet-gold soldered in place.
In general the use of soldering was common for gold objects, and mechanical joints were more rare, which is exactly the opposite to the situation with copper alloy objects. In general the solders used on gold appear to have been made by adding extra silver, copper or both to some of the gold being worked. For example, one Late Period piece (private collection) was of 92 per cent gold with 7 per cent silver and 1 per cent copper, while the solder used to assemble it was 55 per cent gold, 18 per cent silver and 27 per cent copper.
For finer joints, a soldering process which in essence produced solder within the joint area by reducing a copper compound to copper (colloidal hard soldering or diffusion bonding) was probably used from an early period. A mixture of glue and ground malachite (copper carbonate) as used as a pigment, or verdigris, would have sufficed. The glue held the gold components together until the application of heat burnt the glue to carbon. In the presence of carbon the copper compound was reduced to pure copper which then alloyed with, and diffused into, the adjoining gold, thereby fusing the parts together. This type of technique was probably used for much of the granulation work in ancient times, that is the application of fine lines or patterns in minute gold spheres on a sheet-gold background. However, recent study of an example of Middle Kingdom granulation (Ogden 1992b: 52 UC6482), revealed the apparent use of a silver-based solder alloy, the mode of employment of which is not yet understood.
Granulation first appeared in Egypt during the Middle Kingdom and, particularly in view of some of the earliest examples, was almost certainly an imported idea. It reappeared in the middle to late New Kingdom and was used for some Ramesside jewellery. It is all but unknown among the Third Intermediate Period gold-work from Tanis. Granulation work never seems to have been accepted for use in the more traditional, ‘iconographic’ Egyptian jewellery forms and was perhaps always at least partly seen as a `foreign’ technique.
Page 166
In the archetypal, traditional jewellery from Egypt, the forms were high symmetrical, laden with subtle and not-so-subtle imagery and meaning, and inlays of coloured stones were employed more as blocks of pigment than as gems. This means that stones or coloured glass were cut to fit the settings, while the settings were seldom made to employ particularly choice stones. One interesting exception to this rule is a spectacular Twentieth-Dynasty gold bracelet set with a large, irregular piece (perhaps a polished nugget) of turquoise, now in Hildesheim (Pelizaeus Museum, on loan from the Niedersachsische Sparkassenstiftung; Eggebrecht 1996: 76, fig.?*
Even pigment was sometimes applied to gold. In one case examined by the writer, a gold and silver Isis crown from a Third Intermediate or Late Period figure had part of the gold background painted red by the application of red iron oxide pigment over a very thin gesso layer (unpublished, private collection). The use of the red mercury pigment cinnabar has recently been reported on gold-work from the classical world (Williams and Ogden 1994) and in Iberio-Phoenician goldwork of about the fifth century BC (unpublished, private collection).
Enamel is glass which is ground up finely, placed in a hollow, cavity or `cell’ in the metal-work and then heated until it melts and fuses in place. Since the Egyptians were conversant with glass manufacture at least from the early New Kingdom onwards (see Chapter 8, this volume), we might well expect enamel to have been employed in Egyptian gold-work. Use of enamel in various ancient Egyptian objects has been proposed and rejected during the twentieth century (Lucas 1962: 116-17; Aldred 1971: 221 and description to plate 103; Teeter 1981: 319). The only Egyptian gold objects of Dynastic date that are known to the writer and believed likely to be decorated with true enamel are two objects found in the Third Intermediate Period tomb of Wendjebaendjed at Tanis (Ogden 1990/1). The first object is the gold bowl (Montet 1951: 83 and pl. 54; Yoyotte 1987: no. 79). Here the decoration in the centre is an inset rosette motif in the form of a complex rosette (a detail of this is shown in his figure 2). The identification is supported by the similarity in terms of both design and colour palette (white, green and a purplish colour) of a group of six enamelled gold rings found in a Mycenaean tomb at Kouklia (Maryon 1971: 170—I). The other object is one of the pectorals (Montet 1951: 77 and pl. 5o; Yoyotte 1987: no. 75). The predominant use of bluish-green in this pectoral is contrary to Egyptian custom, but not surprising with enamel, where red was problematic to produce. Examination of the pectoral strongly suggest that the inlay material is fused in place, certainly it follows very precisely the contours of the cells (particularly the irregularities of the corners), and in places it seems to overlap with the cells.
Even if these two objects are enamelled — and the now-empty wire-bordered tail feathers of Rameses’ famous duck bracelets (Cairo CG52575/ 6) are other possible candidates —enamelling was certainly the exception rather than the rule in ancient Egypt, other than in Meroitic (Ogden 1989) and
Ptolemaic contexts. Over the years, various reasons have been put forward (e.g. the absence of lead in Egyptian glass, see Dillon 1907), but a simple explanation might be the close melting ranges of the ancient glasses and the ancient gold alloys used in Egypt. The types of glass used in ancient Egypt had melting temperatures that generally ranged between about Boo and 95o °C, and in practice a temperature around 900-1,000 °C would be necessary for fusing a good enamel. The majority of the gold alloys used by the ancient Egyptians would begin to melt between about 900 and 1,050 °C and some of the solders used would start to melt at well under 900 °C. In practice, Egyptian gold jewellery objects could not be enamelled without the very real risk —in many cases the likelihood — that the gold components would start to distort and even begin to come apart.
The enamelling of copper alloys is also encountered from the Third Intermediate Period onwards, but there has been no systematic study to date.
Iron
There are abundant supplies of iron ore in various parts of Egypt and in the Sinai peninsula (Lucas 1962: 235-6; elHinnawi 1965: 1497-509). Iron ores (including magnetite and haematite as well as accessory minerals such as red jasper) are found at Wadi el-Dabba in the Eastern Desert (Akaad and Dardir 1978). Bahariya Oasis in the Western Desert, almost on a latitude with el-Minya, is an important iron-ore source today, supplying haematite, limonite and goethite. El-Baz (1984) provides a good recent bibliography for the iron ores of this region as well as of others such as the iron ores in Aswan sandstone. However, these ore deposits were seemingly seldom if ever exploited in Dynastic times for anything other than pigments (see Chapter 4, this volume) and, we must assume, fluxing agents for copper smelting.
Garland and Bannister refer to old workings at Wadi Abu Gerida in the north Eastern Desert, but these are probably of Roman date (Garland and Bannister 1927: 85). Petrie identified two metal-working sites, possibly for iron smelting, in the Delta — at Naukratis and Tell Defena (Daphnae). He refers to `the large quantity of iron slag found at Naukratis and occasion [sic] pieces of specular iron ore’, dating to the sixth century BC, (Petrie 1886: 39), and he also mentions an `astonishing’ amount of slag — plus a crucible base with slag and charcoal intact — from Defena (Petrie 1888: 79). It is important to remember, however, that copper smelting can also produce a copious amount of iron slag.
Ancient iron can derive from fortuitous examples of meteoric iron (some of which weigh in excess of 3o tonnes), from native iron (telluric iron), or from smelted iron ores. The occasional use of meteoric iron is probably common to most early societies but meteoric iron did not provide a reliable and constant source of supply to early Egypt.
Page 167
The identification of meteoric iron artefacts in Egypt is not straightforward. The usually quoted distinction between meteoric and smelted iron is a relatively high nickel content in the former. However, nickel-containing iron can derive from some smelted ores and long buried meteoric iron artefacts can have much, if not most, of the nickel leached from them. Hence Craddock has recently said that
Some of the well-known small pieces of predynastic and early dynastic corroded iron from Egypt are totally devoid of nickel, but are almost certainly meteoric in origin despite Lucas’s statement to the contrary. (Craddock 1995a: 104 and 256; contra Lucas 1962: 237-8).
Other examples, such as Predynastic sheet-iron beads (Lucas 1962: 237), are reported to contain 7.3 per cent nickel.
Telluric iron is very rare world-wide and, according to a recent survey by Craddock (1995a), only an occurrence on an island off Greenland was definitely exploited in the past. We must thus assume some confusion of terms in Scheel’s suggestion that telluric iron was imported into Egypt from the Peloponnese and from the Near East and that tools of telluric iron appeared during the Saite period (Scheel 1989: 17).
The availability of iron on anything but a fortuitous or sporadic scale had to await the development of iron smelting. The relatively late adoption of this technology owes more to the complexities of the processes than to a lack of supplies, since iron ores are actually abundant world-wide. Iron production requires temperatures of around 1,10o1,150 °C, about the same as for copper smelting.
The initial result of smelting iron ores is a mixed mass of iron, slag and other materials. This has to undergo repeated heating and hammering before relatively high purity and usable wrought iron was left. Such iron could be easily hammered into shape (with repeated annealing to keep it workable) and joined by hammer-welding at temperatures around Lioo °C. Wrought iron of this type could be made into serviceable tools and weapons but had little if any advantage in terms of hardness or ability to take a good edge over copper alloys. About its only noticeable benefit was its tendency to bend not break.
The scattered, supposedly early, ancient Egyptian examples of iron artefacts were possibly metallurgical curiosities as much as evidence of general cultural attainment although they have attracted considerable interest over the last century. Amongst the earliest examples are simple beads made of hammered and bent sheet of Predynastic date found at Girza and examined by Gowland and Desch (see Lucas 1962: 237). The most celebrated instance is the supposed iron sheet found in 1837 near an air passage in the Fourth-Dynasty Great Pyramid at Giza, deep within the masonry and revealed after blasting.
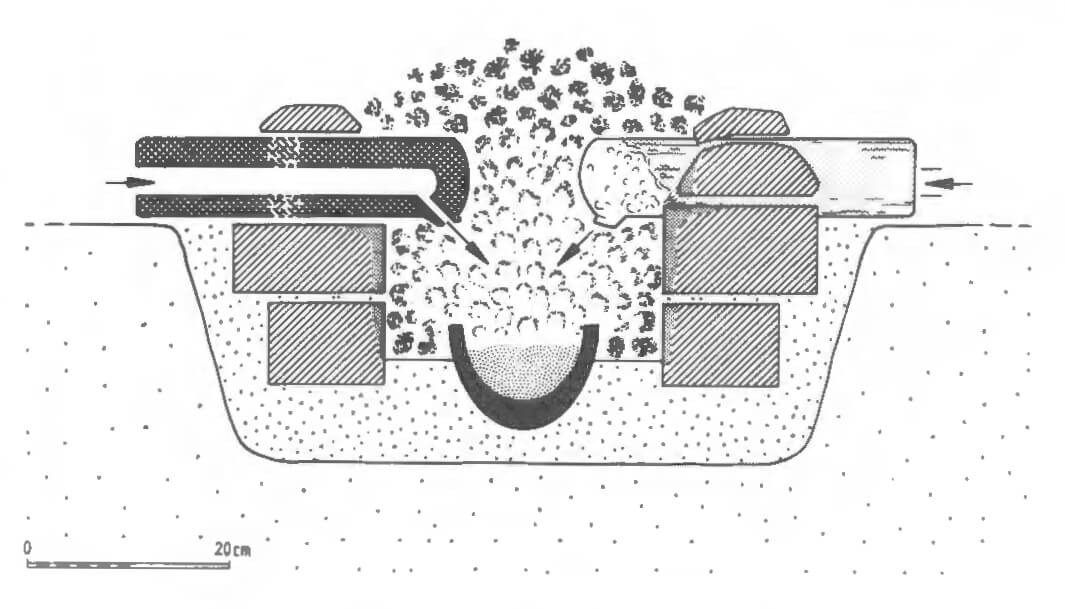
The age of this piece has been the subject of much discussion – for example, changed his mind about its origin, finally coming down on the side of a non-ancient origin (Lucas 1962: 237).
A few years ago this piece was examined metallurgically and an early date again championed (el-Gayar et al. 1989c: 75-83). At the same time, Craddock and Lang expressed some doubts and recently published a full reassessment which concluded that the structure and composition of the iron ‘strongly suggested that the plate of iron from the Great Pyramid is of no great antiquity’ (Craddock and Lang 1989; 1993).
Few would agree with the opinion expressed by Garland and Bannister (1927: 104) that ‘iron chisels were in use by the Fourth Dynasty’, but it seems likely that a handful of iron objects might have existed from the Old Kingdom onwards. Of the various cited ancient examples, it is difficult to confirm chronology or provenance in most cases. Since small pieces of iron could be by-products of copper smelting using an iron oxide flux, the occasional presence of iron from the early Old Kingdom onwards is only to be expected. Generally speaking, there was some sporadic smelting of iron ores, and production of wrought iron, in the ancient Near East as far back as the third millennium BC, perhaps centred on Eastern Anatolia.
The impetus for iron production might well have derived from copper smelting. It is noted above that iron minerals were added to copper ores as fluxes to aid the smelting process. These could result in copper-iron alloys. However, iron with more than a minute trace of copper becomes unworkable and the true link, if any, between copper and iron production remains in doubt. Another possible link is between the introduction of red iron-based glazes, such as the red faience that appears in New Kingdom Egypt, and the development of iron ore smelting.
By the second half of the second millennium BC, iron was beginning to come into more common use, perhaps mainly deriving from the Hittite world. Documents of the period, such as the Amarna Letters, recount the fine iron objects including daggers received at the Egyptian court from foreign rulers (Lucas 1962: 24o). Ofthe rare surviving New Kingdom Egyptian examples, the most famous is the
Page 168
dagger from the tomb of Tutankhamun (Lucas 1962: 239; Carter No. 256k), with its elaborate gold hilt supporting a finely worked iron blade. Another, less spectacular, example is the miniature headrest amulet also from Tutankhamun’s tomb (Lucas 1962: 239).
Steel was being produced in parts of the ancient Near East by the dosing centuries of the second millennium BC (Craddock 1995: 258-9). A process termed ‘carburisation’ adds carbon to the iron which thus provides a ‘steel’ which can be quench-hardened and tempered to considerable hardness. There are sporadic examples from about the middle of the second millennium BC onwards. Studied examples include a pick from Palestine, identified as carburised, quenched and tempered which has been securely dated to the twelfth century BC (Davis et at. 1985: 41-51). The technique of hammering together layers of carburised and uncarburised iron produces a strong tool and examples have now been identified from various parts of the Middle East. Perhaps the earliest Egyptian example is an iron knife in the Petrie collection (Carpenter and Robertson 1930: 428-30). This was initially dated to the late New Kingdom, but a date in the ninth century BC might be more likely (Muhly et at. 1977).
By the middle of the first millennium BC the production of iron had increased dramatically, but the exception appears to be Egypt. Indeed the supremacy of iron weapons over the copper-alloy ones has been seen as a major factor in the Persian conquest of Egypt. Moorey has recently noted that iron only became a cheaper metal than copper in Mesopotamia in the Neo-Babylonian Period, that is around Goo BC (Moorey 1994: 263) — the time of the Persian invasion of Egypt. It is perhaps not surprising that the largest group of iron objects from Egypt from this period is a set of almost two dozen iron woodworking tools found in the Delta in association with a Western Asiatic bronze helmet. This group dates to the seventh century BC (Petrie 1897: 18-19, 1909: 1°6; Williams and Maxwell-Hyslop 1976: 283-305). Four of these tools are steel. Craddock has recently largely dispelled any doubt as to the authenticity of the group (Craddock 1995: 259). It also seems likely that hafted hammers were introduced into Egypt in the Late Period. Hot-working iron with the earlier Egyptian handheld hammers would have been an unpleasant experience.
With additions of between about 2 and 5 per cent carbon, the melting temperature of iron drops to around 1,200 °C and the result is cast iron. Cast iron has little relevance for the ancient Old World and can seemingly be ignored as far as Dynastic Egypt is concerned.
Lead
Native lead is extremely rare, but lead is relatively easy to produce from the main ores galena (lead sulphide) or cerrusite (lead carbonate). Lead can be smelted from galena using a simple charcoal or wood fire.
As Moorey (1994:292) has recently noted, these ores are of readily attractive metallic appearance and would have been easily spotted by early prospectors. Garland and Bannister (1927), as well as Lucas (1962), give the main ancient Egyptian source as Gebel Rosas (Arabic for ‘lead mountain’) south of Quseir on the Red Sea coast. Galena and cerussite were worked here in the early twentieth century and Garland and Bannister refer to ancient workings in the region (Garland and Bannister 1927: 31). There are, however, numerous other ore localities scattered through Egypt, almost down the entire length of Egypt’s Eastern Desert. For example both cerrusite and galena are found at Urn Gheig and Samiuki (Bishay et at. 1974: 47-53). Hassan and Hassan (1981) have recently published a map of some of the lead ore sources in the Eastern Desert accessible via the Wadi Hammamat, while Stos-Gale and Gale (1981) have provided a list of Eastern Desert galena deposits.
In some parts of the Old World, lead was being extracted from its ores during the sixth and even seventh millennia BC. The smelting of lead thus probably pre-dated the smelting of any other metal, copper induded. Perhaps the oldest lead object so far published from Egypt is a hollow figure of a hawk — or perhaps hawk figure casing — found by Petrie in Grave 1257 at Naqada dating to the fourth millennium BC (Ashmolean 1895.137). This has sometimes been described as silver, but recent analysis vindicates Petrie’s original view that it is lead, indeed of remarkable purity — 99.99 per cent lead with only minute traces of silver (about 0.025 per cent), antimony, arsenic, gold and copper (Gale and StosGale 1981). The remarkably high purity of the hawk is matched by an unusual lead figure said to have been found at Abydos and obtained by the British Museum (BM EA99.10-11.1188) in 1899 (Krysko 1986). This figure appears to have had its detail, if not its entire form, produced by carving not casting. The surface patina is perhaps evidence of great age, but further study is required to establish its antiquity.
Lead objects seem to have become more common after the beginning ofthe New Kingdom (Garland and Bannister 1927: 3o) for castings, for functional uses such as for filling weight, and as additions to copper alloys (see p. 154-5). This might relate to the increasing import of metallic lead into Egypt from the New Kingdom onwards.
Tin-lead alloys (pewter) are rare anywhere in the ancient world prior to the later part of the Roman Period (see p. 171). One possible New Kingdom example is discussed below under ‘tin’.
More research on lead ores within Egypt is dearly needed before galena or lead sources can be clarified. One confusing factor in the past with regard to lead isotope provenance studies has been uncertainty as to whether silver was primarily derived from galena in antiquity (see pp. 170-71). It is not impossible that the galena used in mineral form for eye-paint and the like, was largely derived from Egyptian mines, while metallic lead was more typically imported, even from quite early times.
Page 169
There is a huge literature on the isotopic characterisation of ancient Egyptian lead and lead-containing alloys (including copper alloys and silver) and the reader is directed to the relevant geological and Egyptological bibliographies and literature (el-Baz 1984; Stos-Gale 1995; Hassan and Hassan 1981). In theory, the ratios of the various isotopes of lead can ‘fingerprint’ a source and thus permit objects to be traced to their origin. Some researchers, however, are more pessimistic about the real potential for mine identification (Budd et al. 1995: 143-50). The research to date on Egyptian material is confusing, both local and imported lead and lead ores would have appear to have been used and the final word on the subject has by no means been written.
Mercury
Mercury is a silvery metal that is liquid at temperatures above —38.87 °C. It was first observed solid on the intensely cold Christmas day in St Petersburg in 1759. There is no evidence for the use of metallic mercury in Pharaonic Egypt, but the use of mercury compounds for other purposes is possible. Cinnabar (bright red mercuric sulphide) does occur in Egypt (Sabet et al. 1976b). In several parts of the ancient Old World there is evidence for its use as a pigment by about the fifth century BC (see p. 166), and it has even been reported that it was in use in Mesopotamia in the third millennium BC (Moorey 1994: 155).
Mercury combines with gold and silver to form semiliquid amalgams. These can be applied over metal surfaces as a plating; the mercury is vaporised off and the resulting gold or silver layer polished or burnished. There is little evidence for this process before Hellenistic times and the earliest examples from Egypt are a handful of ornaments of the Ptolemaic period, and in the Classical rather than Egyptian idiom (Williams and Ogden 1994).
Platinum metals
The platinum group of metals includes platinum itself, as well as palladium, ruthenium, iridium, osmium and rhodium. Small grains composed of various alloys of these metals (with mineralogical names such as osmiridium, iridosmine, rutheniridosmine etc., depending on composition) frequently occur in alluvial gold deposits. Due to their hardness, specific gravity and chemical inertness, they often remain with the gold throughout the separation and metal-working processes. The grains composed primarily of various proportions of osmium, iridium and ruthenium remain as hard white metal specks in the final goldwork. Such specks, varying from microscopic to several millimetres long, are commonly visible in many categories of ancient goldwork, including those from ancient Egypt (Ogden 1976, 1977).
Inclusions of this type have been noted in Egyptian gold by various authorities during the twentieth century (Ogden 1976), and Petrie was perhaps the first to describe them accurately, terming the inclusions in a Middle Kingdom gold scarab ‘osmiridium’. Williams (1924) less precisely called such inclusions ‘platinum metals’ and Lucas (1962) was incorrect in assuming them to be ‘largely platinum’. In more recent years, advances in analytical techniques have permitted the in situ analysis of many such inclusions in Egyptian and other gold (Ogden 1976, 1977; Meeks and Tite 1980). These analyses show that they are indeed predominantly osmium and iridium, sometimes with considerable ruthenium, and less commonly with some rhodium. Platinum occurs as little more than traces and palladium has not yet been detected.
The commonness of such specks in Egyptian goldwork indicates that the platinum group metal grains are common in the gold deposits exploited by the Egyptians and thus must almost certainly occur in the gold deposits of the Eastern Desert or Nubia. There has been no geological confirmation to date of any platinum metal occurrence in the Eastern Desert, although it is possible that it may exist in this region (see Ogden 1976), given the fact that:
- there are well-known (and recently exploited) platinum metal occurrences with gold in what is now Ethiopia;
- there is platinum in nickel ores from the island of Zabargad (St John’s Island) in the Red Sea, about eighty kilometres southeast of Berenike; and
- there is an unconfirmed report of such metals in the
Platinoid inclusions have been noted in Egyptian gold-work as early as the Old Kingdom, not so far before that. The inclusions are seen in many gold objects from Egypt from then on to the Roman Period and are typically primarily iridium-osmium-ruthenium alloys. However, the average proportion of ruthenium present seems to drop from the Middle Kingdom onwards, from over 25 per cent to under that amount, perhaps indicating a significant switch in gold mining region (Meeks and Tite 1980), mine type or perhaps even recovery processes.
In the nineteenth century, Berthelot (1900) identified the inlay in an Egyptian copper-alloy box as some sort of platinum metal alloy. It is not improbable that a composite platinum nugget, like those recorded more recently in Ethiopian streams, was inadvertently used instead of an electrum one (Ogden 1977). A new examination of this inlay would be useful.
It is generally assumed that platinum metal grains only occur in alluvial, not vein gold, deposits. It is true that the combination of gold and platinum metals is all but unknown in primary reef gold deposits, but combinations are found in some secondary deposits and it is not unusual for gold and platinum metal-bearing rocks to occur in proximity.
Page 170
Platiniferous rocks transverse auriferous quartz at Yubdo in Ethiopia and similar associations are perhaps likely further north. The presence of chromite deposits in areas adjacent to gold mining areas (cubic chromite inclusions are also visible in some Egyptian steatite) and the auriferous quartz veins traversing serpentinite rock at the el-Sid/Baramia gold mining area of the Eastern Desert could, from a geological point of view, point to platinoids being present with gold retrieved using ancient vein gold exploitation technology (Sabet et al. 1976a; Ogden 1977).
Silver
Lucas’ suggestion that much Egyptian silver, particularly that of the earlier periods, was actually a natural alloy of silver and gold has been substantiated by recent studies by Gale and Stos-Gale (1981) and Mishara and Meyers (1974). This was presumably natural ‘aurian silver’ from Egyptian and Nubian ‘gold’ mines.
However, some silver with 1 per cent or less gold occurs from Predynastic times onwards. Since silver could not be separated from natural gold/silver alloys so early, the silver must derive from mineral ores. This is certainly implied by the small lead presence in such silver (Gale and Stos-Gale 1981).
There was, perhaps, some exploitation of silver ores such as argentite (silver sulphide) in antiquity but most of the silver probably derives from lead ores. When lead ores are smelted, the molten lead produced contains any traces of silver. When this lead is heated under strong oxidising conditions the lead is converted to litharge — lead monoxide — and the silver will be left as a shining globule of silver. This oxidising process is termed cupellation and was a process also used to remove base metals from silver and gold. As we saw above, lead was being smelted in some parts of the Old World by the seventh or sixth millennium BC, and analysis of Egyptian objects suggests that it was in use, on at least occasions, well before about 3000 BC.
It has often been assumed that the prime such source was the lead ore galena (lead sulphide) which does, indeed, contain some silver. However the silver levels in Egyptian galena are generally low (for ancient exploitation methods) and over recent years analysis, studies of early documentary evidence and experimentation, have indicated that the commonest sources of silver in antiquity might rather have been the oxidised lead ores, particularly cerussite (lead carbonate). Silver obtained from cerussite typically contains the noticeable amounts of gold and other trace elements that are typical of so much silver from antiquity. We can also note that silver right up to recent times usually contains a noticeable lead content. For the purposes of isotope provenance studies (see p. 168) it is vital to note that this lead need not always derive from the ores themselves, but might well represent the lead added during a refining process.
One of the earliest silver objects from Egypt is a box-lid from Naqada which dates to the middle of the fourth mil lennium BC (Ashmolean 1895.987).
However, a recent analysis shows this to contain about 15 per cent gold and it is thus almost certainly aurian silver from a gold mine (Gale and Stos-Gale 1981). Nevertheless, the lead hawk casing mentioned above is perhaps evidence for a fairly sophisticated lead/silver production centre in this area during the fourth millennium BC. There is some debate as to whether the lead ores of Egypt’s Eastern Desert have silver contents high enough for successful ancient exploitation (Garland and Bannister 1927: 31; Gale and Stos-Gale 1981). Certainly, so far, lead isotope analysis of ancient Egyptian silver objects has not supported an indigenous origin.
Recent analyses of various of the vessels and ingots in the Middle Kingdom ‘el-Tod treasure’ reveal relatively pure silver with gold concentrations generally under 0.2 per cent, (maximum about o.65 per cent), lead well under 1 per cent and generally under 0.2 per cent (Menu 1994: 29-45). Many of the objects have only minute traces of copper, but up to 4 per cent copper in some objects suggests occasional intentional alloying for practical working reasons. The silver was obtained by the cupellation of an argentiferous mineral, and lead isotope studies show that the silver was almost certainly imported and a northern Greek or south Anatolian origin is possible. Most recently Maxwell-Hyslop has argued that it is quite likely that the el-Tod assemblage was collected by a ruler in north Syria and sent from there to Egypt (Maxwell-Hyslop 1995). The cylinder seals found with the treasure would support this (Porada 1982).
A Middle Kingdom silver mount from a scarab has a copper level of 26.4 per cent, and Lucas quotes another object with about 66 per cent copper to 34 per cent silver (1962: 249). However, in general copper levels in silver and aurian silver rarely exceed about io per cent and over 1 or 2 per cent is probably deliberate. A New Kingdom silver ring supposedly with about 15 per cent tin present is hardly surprising in view ofthe colour similarities ofthe two metals but more research is needed on this piece (see p. 171).
Silver was worked in much the same way as copper alloys. Sheet-metal objects were generally hammered and raised to shape, while three dimensional figurines could be cast by the lost wax process (see above under ‘copper’). Fine examples of silver from the New Kingdom include a trumpet and pomegranate vase from the tomb of TutanIchamun. Once silver became less exceptional in Egypt, it could be used in great quantities — in the Ramesside Period we hear of enormous weights of silver statuary dedicated in the temples (Becker et al. 1994: 54 n. 31). However, few have survived — one such is a superb, hollow-cast silver statuette of a pharaoh presenting a figure of Maat (Louvre E27431, Ziegler 1988). Other surviving silver objects of this period include the magnificent silver vessels in the Ramesside `Bubastis treasure’ (for a summary and references see Ogden 1990/1). Indications of the later abundance of silver include the silver sarcophagi of the Tanite pharaohs (see Yoyotte 1987).
Page 171
Silver statuettes of deities or royal figures are rare. Recently Becker et at. (1994) have listed and illustrated several of these in their comprehensive publication of a fine silver statuette of a naked woman of the Saite Period, now in the Metropolitan Museum of Art, New York. This piece was made of high purity silver (about 96.7 per cent silver, 2.6 per cent copper) as a casting with separately applied wig and necklet. The cast torso has small square silver plugs correcting casting flaws.
We cannot always assume that ancient silver was intended to have a bright, shiny surface. The deliberate production of a black surface on Classical silver objects has been the subject of some debate in recent years while in the ancient Near East some such tradition is implied by the Talmudic ruling against burning sulphur on the Sabbath to blacken silver. During the conservation of the fine silver Saite naked woman described above, the conservators found ‘Black tabular hexagonal crystals in close contact with the silver . . . may be a silver sulphide, although this is rare in archaeological contexts.’ (Becker et at. 1994). This black sulphide could perhaps be interpreted as an original deliberate surface. If so, the ‘unusual feature’ of the raised rather than incised cartouches on the arms would be explained — they would look magnificent in shiny silver against a black background. We can also note that the investigators found traces of a bright red substance on the wig that appeared to be composed of iron, calcium and silicon. This brings to mind the red iron oxide pigment over a very thin gesso layer noted by the writer on an Egyptian gold headdress (see p. 166).
Tin
Tin is a soft, light, silvery white metal that is obtained either as a native metal or derived from various ores — most commonly, if not invariably in antiquity, cassiterite (Earl 1994). Despite the use of tin as an alloying material in copper alloys from the Middle Kingdom onwards, most earlier authorities have expressed a belief that tin ores do not occur in Egypt (Garland and Bannister 1927: 4). However, there are deposits of cassiterite, some of high grade, in the Eastern Desert and some tin is commercially mined there today (Sabet et al. 1976c). There are also deposits of chalcocite in Sinai (Muhly 1978), and Wainwright reported placer tin deposits at Nahr Ibrahim (Wainwright 1934, 1943-4). Undoubtedly some tin was being imported into Egypt in antiquity, but probably not all of it.
Early tin objects from Egypt are extremely rare — perhaps suggesting that tin was generally employed in the copper and other industries in the form of mineral ores, not as metal. One recently studied exception is a small sheet tin bead from tomb 37 at Assasif, roughly contemporary with Thutmose III.
Analysis showed this to be of high purity tin with just o.6 per cent lead, 2.1 per cent copper and 0.4 per cent iron (Lilyquist and Brill 1993: 65). Interestingly the lead isotope ratio of this bead has led to the tentative suggestion that the tin might originate in the Taurus Mountains in southern Turkey, where, indeed tin ore (cassiterite) exists and where there are traces of ancient mining activity dating back to the early Bronze Age (Yener et at. 1989; Earl and Ozbal 1996).
Other early uses of tin indude a ring of late New Kingdom type from Gurob which was analysed by Dr Gladstone and shown to be pure tin (Petrie 1891: pl. 22.10; Garland and Bannister 1927: 29). There is also a well-known flask from a tomb at Abydos (Ashmolean E2442; Petrie 1904: 5o; Douglas 1989). Analysis showed this to be made from an alloy of 95 per cent tin, 4.75 per cent lead, hence it is a low-lead pewter. Tin alloys with around 5 per cent lead —perhaps representing the optimum hardness — are well-known in Egypt and elsewhere from the Roman period onwards. Although the tomb context points to a late New Kingdom origin for the flask (and the basic flattened, two-handled shape can be paralleled in other materials at that period), the possibility that the vessel is somehow intrusive should be borne in mind. The composition and construction — with two horizontal seams — might well point to a later, perhaps even Islamic, origin.
With the exception of the above objects, tin objects are extremely rare in Egypt until Roman times when tin with low lead contents (pewter) became quite common for jewellery, vessels and some other purposes, including solders for copper alloy objects (Williams 1924).
Copper—tin alloys were discussed above with the other copper alloys. We can however note a ring of Nineteenth-Dynasty date analysed by Berthelot which was an alloy of almost 76 per cent tin, with around 16 per cent copper and r per cent lead (Berthelot 1895: 131-46). There is also a ring of possible New Kingdom date which is made of a tin—silver alloy (Williams 1924; Ogden 1983a: 30-1). The appearance of ‘odd’ tin alloys at the time when the Egyptians were, perhaps, first becoming acquainted with metallic tin is not surprising.
Zinc
With the exception of a few possible early, but non-Egyptian, examples, the use of metallic zinc has been limited to recent centuries (Craddock 199o). In the field of ancient Egyptian metallurgy, zinc is only known as a trace element in some copper and lead alloys. Both copper and lead ores in the Eastern Desert can contain zinc. As noted above, the available evidence suggests that zinc was not a deliberate addition to copper or other alloys until Ptolemaic times and, in any case, was added as a zinc ore or compound, not as the metal.
Page 172
The alliance of science
A detailed study of the techniques of analysis now used on ancient metals would be out of place here, besides, much of what has been described in other chapters can apply equally to metals. In briefwe can note that the scientific methods of study as applied to ancient metals include different types of microscopy and various spectrographic and other analysis techniques.
The simple binocular microscope, generally providing well under ioo x magnification allows us to examine technology and surface detail. It is a favourite tool of the conservator and curator. Ownership of, or easy access to, a binocular microscope should be an absolute minimum requirement for any museum department or excavation house.
A metallurgical microscope is used to examine prepared polished surfaces of the metal (typically etched to reveal internal structure). This type of microscope is generally used at higher magnifications (several hundred times in practice) and allows us to deduce much about composition, mode of manufacture, homogeneity and corrosion and ageing effects. Generally speaking, only a small, prepared sample taken from the object can be examined. A scanning electron microscope, which relies on electron beams not light, gives a much greater range of magnification (up to many thousand times) and a good depth of focus. However, constraints include the high capital and running costs and size, and also the need to place the observed item in a vacuum chamber which means that only relatively small items or samples removed from objects can be examined.
A major advantage of the scanning electron microscope is the frequent presence of in-built analytical features. Such analysis is usually based on x-ray fluorescence. Here, with the help of computers, the characteristics of the x-rays generated when an electron beam strikes the sample surface tell us what elements are present and, with varying degrees of accuracy, their relative proportions. This type of analysis is ideal for homogeneous materials or for small discrete areas such as plated layers, solders, joins and inclusions or various phases in metals. A disadvantage is that many metals, including copper alloys can be very inhomogeneous. Lead, for example, remains as discrete ‘lakes’ in copper alloys, and a series of ‘point’ analyses on a leaded copper alloy could easily show compositions ranging from no lead to almost ioo per cent lead! So, either a series of analyses must be made to give a likely average composition, or some other technique must be used which requires a more representative sample area or size.
Two techniques commonly used today on metals include atomic absorption (AA) and inductively coupled plasma spectroscopy (ICP). For the details of these and other techniques, the reader is directed to the relevant scientific and archaeometric literature. In essence, these are modern versions of traditional spectrographic processes whereby the composition is determined from the light or other radiation generated by burning or vapourising a small sample. For AA or ICP a small sample is required
and this is typically the powder produced by drilling a hole with a I mm or 0.5 mm drill. This is hardly disfiguring to the vast majority of archaeological artefacts and the archaeologist or site authority who refuses a 1 mm hole on an object, when that object was itself revealed by digging a five-metre trench through an occupation site, can hardly claim to have logic, let alone archaeological best interest, on their side.
The scientific study of metal objects is a huge and potentially very informative field. The scope can range from microscopic observation in order to determine assembly techniques of gold jewellery to x-ray diffraction studies to identify corrosion products on copper alloys. No one person, whether scientist or archaeologist, can be au fait with all the disciplines applicable to ancient metals. However, excavators and curators should at least be aware of the type of information that can be gained by scientific study, should know what questions to ask of the scientists and, during excavation and post-excavation work, feel obliged to consider what can and should be done to facilitate the full study of the metal objects they find.
References
Akaad, M.K. and Dardir, A.A. 1978. The iron ore deposit of Wadi el-Dabbah, Eastern Desert, Egypt. Precambrian Research, 6/1: A6—A7.
Aldred, C. 1971. Jewels of the Pharaohs. London: Thames and Hudson.
Anwar, Y.M. 1964. Note on the occurence of copper minerals at Ras Benas, Eastern Desert. Journal of the Geological Society of Egypt, 8/2: 89-94.
Azer, N. 1966. Remarks on the origin of Precambrian mineral deposits in Egypt (UAR). Tschermaks Mineralogische and Petrographische Mitteilungen, Drittefolge 2: 41-64.
Bachmann, H.-G. 1980. Early copper smelting techniques in Sinai and in the Negev as deduced from slag investigation. In Scientific Studies in Early Mining and Extractive Metallurgy (ed. P.T. Craddock). British Museum Occasional Paper 20. London: BMP, pp. 103-4.
Bass, G. 1986. A Bronze Age shipwreck at Ulu Burun (Kas): 1984 campaign. AJA, 9o: 269-96.
Baumgartel, E.J. 1960. The Cultures of Prehistoric Egypt II. Oxford: OUP.
el-Baz, F. 1984. The Geology of Egypt: An Annotated Bibliography. Leiden: Brill.
Becker, L., Pilosi, L. and Schorsch, D. 1994. An Egyptian silver statuette of the Saite Period — a technical study. Metropolitan Museum Journal, 29: 37-56.
Beit-Arieh, 1.1981. An Early Bronze Age II site near Sheikh ‘Awad in Southern Sinai. Tel Aviv, 8,2: 95-127.
1985. Serabit el-Khadim: new metallurgical and chronological aspects. Levant,17: 89-116.
Berthelot, M. 1895. Etudes sur les metaux. In Fouilles d Dahchour (J. de Morgan). Vienna: Adolphe Holzhausen, pp. 131-46. 1900. Sur les metaux egyptiens: etudes sur un etui metallique
Page 173
et ses inscrptions. Monuments et Memoires (Fondation Eugene Piot) 7: 121-41.
Bishay, A., Naim, G., Amin, H. 1974. Zinc-lead deposits. Geological Survey of Egypt Paper 61: 47-53.
Brunton, G., Gardner, E.W. and Petrie, W.M.F. 1927. Qau and Badari I. London: BSAE.
de Bruyn, P. 1955. A graffito of the scribe Dhuthotpe, reckoner of gold, in the south-eastern desert. JEA, 41: 121-2.
Budd, P., Pollard, A.M., Scaife, B. and Thomas, R.G. 1995. The possible fractionation of lead isotopes in ancient metallurgical processes. Archaeometry, 37/I: 143-50.
Caley, E.R. 1964. Analysis of Ancient Metals. Oxford: Pergamon. Carpenter, H.C.H. 1932. An Egyptian axe head of great antiquity. Nature, 13o: 625-6.
Carpenter, H.C.H. and Robertson, J.M. 1930. The metallography of some ancient Egyptian implements. Journal of the Iron and Steel Institute, 121: 428-30.
Chappaz, J.-L. 1983. Working with gold in ancient Egypt. Aurum, 14: 34–40.
Coghlan, H.H. 1975. Copper artefacts from Tutankhamun’s tomb. Journal of the Historical Metallurgy Society, 9/2: 64-7.
Constantinou, G. 1982. Geological features and ancient exploitation of the cupiferous sulphide orebodies of Cyprus. In Early Metallurgy in Cyprus, 4000-500 BC, (eds. J.D. Muhly, R. Maddin and V. Karageorghis). Larnaca: Pierides Foundation, pp. 13-23.
Cowell, R.M. 1987. Scientific appendix I: chemical analyses. In Catalogue of Egyptian Antiquities in the British Museum: VII Tools and Weapons I: Axes (W.V. Davies) London: BMP, pp. 96-118.
Craddock, P.T. 1980. The composition of copper produced at the ancient smelting camps in the Wadi Timna, Israel. In Scientific Studies in Early Mining and Extractive Metallurgy (ed. P.T. Craddock). British Museum Occasional Papers 20. London: BMP, pp. 165-76.
1985. Three thousand years of copper alloys: from the Bronze Age to the Industrial Revolution. In Application of Science in Examination of Works of Art Proceedings of the Seminar September 7-9, 1983 (ed. P.A. England and L van Zelst). Boston: MFA, pp. 59-67.
1990. Zinc in classical antiquity. In 2000 Years of Zinc and Brass (ed. P.T. Craddock), British Musuem Occasional Paper 5o. London: BMP, pp. 29-72.
1994. Secrets of Achilles’ shield. New Scientist. 22 January: 32-5.
1995. Early Metal Mining and Production. Edinburgh: Edinburgh University Press.
1998. The black bronzes of Egypt. In Proceedings of the First International Conference on Ancient Mining and Metallurgy and Conservation of Metallic Artifacts. (10-12 April 1995). (ed. F. A. Esmael) Cairo: Ministry of Culture, Supreme Council of Antiquities, pp. 89-119.
Craddock, P.T. and Lang, J. 1989. Letter. Journal of the Historical Metallurgy Society 23/2: 123.
1993. Gizeh iron revisited. Journal of the Historical Metallurgy Society, 27/2: 57-9.
Craddock, P.T. and Giumlia-Mair, A. 1993. Hsmn-Km, Corinthian bronze, shakudo: black-patinated bronze in the ancient world. In Metal Plating and Patination: Cultural, Technical And Historical Developments. (eds. S. La Niece and P.T. Craddock).
Oxford: Butterworth-Heinemann, pp. 101-27.
Craddock, P.T. and Meeks, N.D. 1987. Iron in ancient copper. Archaeometry, 29/2: 187-204.
Davey, C. 1979. Some ancient Near Eastern pot bellows. Levant, II:
Davies, N. de G. 1943. The Tomb of Rekh-mi-re at Thebes. New York: MMA.
Davis, D., Maddin, R., Muhly, J.D. and Stech, T. 1985. A steel pick from Mt. Adair in Palestine. JNES, 44/I: 41-51.
Dayton, J.E. 1978. Minerals, Metals, Glazing and Man, London: Harrap.
Delange, E. 1987. Catalogue des statues Egyptiennes du Moyen Empire. Paris: Musee du Louvre.
Desch, C.H. 1928. Report on the metallurgical examination of specimens for the Sumerian Committee of the British Association. Report of the British Association. London.
Dillon, E. 1907. A neglected point in the early history of enamel, The Burlington Magazine, II: 373-5.
Doonan, R.C.P. 1994. Sweat, fire and brimstone: Pre-treatment of copper ore and the effects on smelting techniques. Journal of the Historical Metallurgy Society, 28 (2): 84-97.
Douglas, J.A. 1989. The Abydos flask enigma. Journal of the Pewter Society 7 (I): 1-2.
Earl, B. 1994. Tin from the Bronze Age smelting viewpoint.
Journal of the Historical Metallurgy Society , 28 (2): 117-120.
Earl, B. and Ozbal, H. 1996. Early Bronze Age tin processing at
Kestel/GOltepe, Anatolia. Archaeometry, 38, (2): 289-303.
Eggebrecht, A. 1993. M6gen sie einen Erinnerung sein fiir die
Nachwelt. In Roemer- and Pelizaeus-Museum (ed. A. Eggeb-
recht). Mainz: von Zabern, pp. 50-9I.
(ed.) 1996. Pelizaeus Museum Hildesheim: The Egyptian Collection. Mainz: von Zabern.
Emery, W.B. 1939. A preliminary report on the First Dynasty
copper treasure from North Saqqara. ASAE, 39: 427-35.
1970. Preliminary report on the excavation at North Saqqara 1968-9. JEA, 56: 5-II.
Fishman, B. and Fleming, S.J. 1980. A bronze figure of Tutan-
khamun: technical studies. Archaeometry, 22 (I): 81-6.
Fleming, S.J. 1982. Lead isotope analyses of Late Period Egyptian
bronzes. MASCA Journal, 2 (2): 65-9.
Fleming, S.J. and Crowfoot-Payne, J. 1979. PIXE analyses of some Egyptian bronzes of the Late Period. MASCA Journal, 1 (2): 46-7.
Frantz, J.H. and Schorsch, D. 1990. Egyptian red gold, Archaeomaterials, 4:133–52.
Gale, N.H. and Stos-Gale, Z.A. 1981. Ancient Egyptian silver. JEA, 67:103-15.
Garland, H and Bannister, C.0.1927. Ancient Egyptian Metallurgy. London: Griffin.
el-Gayar, el-S. and Jones, M.P. /989a. A possible source of copper ore fragments at the Old Kingdom town of Buhen. JEA, 75: 31-40.
1989b. Old Kingdom copper smelting artifacts from Buhen in Upper Egypt. Journal of the Historical Metallurgy Society, 23/I: 16-24.
1989c. Metallurgical investigation of an iron plate found in 1837 in the Great Pyramid. Journal of the Historical Metallurgy Society, 23/2: 75-83.
el-Gayar, el-S. and B. Rothenberg, B. 1998. Predynastic and Old Kingdom copper metallurgy in South Sinai. In Proceedings of
Page 174
the First International Conference on Ancient Egyptian Mining and Metallurgy and Conservation of Metallic Artifacts. (10-12 April 1995) (ed. F. A. Esmael). Cairo: SCA, pp. 147-58.
Giumlia-Mair A.1996. Das Krokodil and Amenemhat III aus el-Fayum. Antike Kunst, 27 / 4: 313-21 and 34o.
Giveon, R. 1977. Egyptian finger rings and seals from south of Gaza. Tel Aviv, 4/1-2: 66-70.
el-Goresy, A., Schieg,l, S. and Weiner, K.L. 1998. A chronological scheme for the technological evolution of copper in ancient Egypt. In Proceedings of the First International Conference on Ancient Egyptian Mining and Metallurgy and Conservation of Metallic Artifacts. (10-12 April 1995). (ed. F. A. Esmael) Cairo: Ministry of Culture, SCA, pp. 215-34.
Greaves, R.H. and Little, O.H. 1929. The gold resources of Egypt. Report of the Fifteenth International Geological Congress. South Africa, pp. 123-7.
Hassan, A.A. and Hassan, F.A. 1981. Sources of galena in
Predynastic Egypt at Nagada. Archaeometry, 23/I: 77-82.
Hayes, W.C. 1959. The Scepter of Egypt II: The Hyksos Period and the New Kingdom (1675-1080 BC). New York: MMA.
Haynes, D. 1992. The Technique of Greek Bronze Statuary. Mainz: von Zabern.
Hill, M. 1995. Statuette of Tuthmose III. The Metropolitan Museum of Art Bulletin, 53/2: 6.
el-Hinnawi, E.E. 1965. Contributions to the study of Egyptian (UAR) iron ores. Economic Geology, 6017: 1497-509.
Hume, W.F. 1937. Geology of Egypt II: The Fundamental Precambrian Rocks of Egypt and the Sudan, 3: The Minerals of Economic Value. Cairo: Geological Survey of Egypt.
Jett, P., Sturman, S. and Drayman Weisser, T. 1985. A study of the Egyptian bronze falcon figurines in the Walters Art Gallery. Studies in Conservation, 3o/3: 112-18.
Kaczmarczyk, A. and Hedges, R.E.M. 1983. Ancient Egyptian Faience. Warminster: Aris and Phillips.
Klemm, R. and Klemm, D.D. 1994. Chronologischer Abriss der antiken Goldgewinnung in der Ostwaste Agyptens. MDAIK, 5o: 189-222.
Krysko, W.W. 1986. Comments on the oldest known lead figurine.
Journal of the Historical Metallurgy Society, 20/2:109-u.
Levene, D. 1998. Expedition to Atika. In Proceedings of the First International Conference on Ancient Egyptian Mining and Metallurgy and Conservation of Metallic Artifacts. (10-12 April 1995). (ed. F. A. Esmael) Cairo: Ministry of Culture, SCA, pp. 365-78.
Lilyquist, C. and Brill, R.H. 1993. Studies in Ancient Glass. New York: MMA.
Lucas, A. 1962. Ancient Egyptian Materials and Industries. 4th edn., rev. J.R. Harris. London: Edward Arnold.
Maddin, R., Stech, T., Muhly, J.D. and Brovarski, E. 1984. Old Kingdom models from the tomb of Impy: metallurgical studies. f EA ,70: 33-41.
Markowitz, Y., Lacovara,P. and Hachfield, P. 1997. Jewellery fragments from the tomb of Nefertari in the Museum of Fine Arts, Boston. In Chief of Seers, Egyptian Studies in Memory of Cyril Aldred. (eds. E. Goring, C.N. Reeves and J. Ruffle). London: KPI, pp. 220-8.
Martin, G.T. 1991. The Hidden Tombs of Memphis. London: Thames and Hudson.
Maryon, H.G. 1971. Metalwork and Enamelling. 5th edn. New York: Dover.
Maxwell-Hyslop, K.R. 1995. A note on the Anatolian connections of the Tod Treasure. Anatolian Studies, 45: 243-5o.
Meeks, N.D. and Tite, M.S. 1980. The analysis of platinum-group
element inclusions in gold antiquities. JAS,7: 267-75.
Mellado, E.P. 1995. Egyptian mining in Sinai during the Middle Kingdom. In Abstracts of Papers presented at the Seventh International Congress of Egyptologists, Cambridge 3-9 September 1995. London: EES, pp. 142-3.
Menu, M. 1994. Analyse du tresor de Tod. BSFE, 130: 29-45.
Merkel, J.F. 1995. Egyptian New Kingdom copper smelting -smelting experiments. In Abstracts of the International Conference on Ancient Egyptian Mining and Metallurgy and Conservation of Metallic Artifacts. (10-12 April 1995). Cairo: Ministry of Culture, Supreme Council of Antiquities, p. 22.
Mishara, J. and Meyers, P. 1974. Ancient Egyptian silver: a review. In Recent Advances in Science and Technology of Materials: Proceedings of the Cairo Solid State Conference III (ed. A. Bishay). New York: Plenum Press, pp. 29-45.
Montet, P. 1951. La acropole royale de Tanis II: les constructions et le tombeau de Psousenn45 d Tanis. Paris: CNRS.
Moorey, P.R.S. 1994. Ancient Mesopotamian Materials and Industries. Oxford: OUP.
Moran, W.L. 1992. The Amarna Letters. Baltimore MD: Johns Hopkins University Press.
Morgan, M.H. 1914. Vitruvius: The Ten Books on Architecture. Cambridge MA: Harvard University Press.
Muhly, J.D. 1978. New evidence for sources of and trade in Bronze Age tin. In The Search for Ancient Tin. (eds. J.S. Olin, A.D. Franklin and T.A. Wertime) Washington DC: Smithsonian Institution Press, pp. 43-8.
Muhly, J.D., Wheeler, T.S and Maddin, R. 1977. An iron adze of
the fifth-fourth centuries BC from al Mina. Levant, 9:156-61. Nassim, GL. 1949. The discovery of nickel in Egypt. Economic
Geology, 44: 143-50.
Nibbi, A. 1987. Ancient Egyptian Pot Bellows and the Oxhide Ingot Shape. Oxford: D.E. Publications.
Nofal, A.A. and Waly, M.A. 1998. Foundry technology of ancient Egypt. In Proceedings of the First International Conference on Ancient Egyptian Mining and Metallurgy and Conservation of Metallic Artifacts. (10-12 April 1995) (ed. F. A. Esmael). Cairo: SCA, pp. 175-82.
Oddy, W.A., Padley, T.G. and Meeks, N. 1978. Some unusual techniques in gilding in antiquity. Eighteenth International Symposium on Archaeometry and Archaeological Prospecting. Bonn.
Oddy, W.A., Pearce, P. and Green, L. 1988. An unusual gilding technique on some Egyptian bronzes. In Conservation of Ancient Egyptian Materials, (Preprints of the conference organised by the United Kingdom Institute for Conservation, Archaeology Section, held at Bristol, 15-16 December 1988. (eds. S.C. Watkins and C.E. Browne). London: UKIC, pp. 35–9.
Ogden, J.M. 1976. The so-called ‘platinum’ inclusions in Egyptian goldwork. [ EA , 62: 138-44.
1977. Platinum group metal inclusions in ancient gold artefacts. Journal of Historical Metallurgy, 11/2: 53-72.
1983a. Jewellery of the Ancient World. London: Trefoil.
1983b. Surface changes in buried gold items. Preprints of the
Second International Symposium `Historische Technologie der
Edelmetalle’. 25-28 April, Meersburg, pp. 24-6.
Page 175
1989. Meroitic enamel work in Resumes of papers presented at the Seventh British Museum Enamel Colloquium, (1985), Jewellery Studies, 3: 83-4.
1990/1. Gold in a time of bronze and iron. The Journal of the Ancient Chronology Forum, 4: 6-14.
1992a. Gold in antiquity. Interdisciplinary Science Review, 17/3: 261-70.
1992b. Interpreting the Past: Ancient Jewellery. London: BMP.
1993. Aesthetic and technical considerations regarding the colour and texture of ancient goldwork. In Metal Plating and Patination: Cultural, Technical and Historical Developments, (eds. S. La Niece and P.T. Craddock). London: Butterworth-Heinemann, pp. 39-49.
1994. Black bronze and woven gold. Gem and Jewellery News, 3/2: 24-5.
Oldfather, C.H. 1935. Diodorus Siculus: The Library of History. Loeb Classical Library. Cambridge MA and London: Harvard University Press and Heinemann.
Ortiz, G. 1994. In Pursuit of the Absolute: Art of the Ancient World. London: Royal Academy.
Osman, A. 1995. Ancient gold mining in Egypt and its geologic aspects. In Abstracts of the International Conference on Ancient Egyptian Mining and Metallurgy and Conservation of Metallic Artifacts. (10-12 April 1995). Cairo: Ministry of Culture, Supreme Council of Antiquities, p. 8.
Petrie, W.M.F. 1886. Naucratis I:1884-5. London: EEF.
1888. Tanis II. London: EEF.
1891. Illahun, Kahun and Gurob 1889-90. London: Nutt.
1897. Six Temples at Thebes. London: Quaritch.
1904. Abydos III. London: EEF.
1906. Researches in Sinai. London: John Murray.
1909. The Arts and Crafts of Egypt. Edinburgh: Foulis.
Porada, E. 1982. Remarks on the Tod treasure in Egypt. In Societies and Languages of the Ancient Near East: Studies Presented in Honour of I.M. Diakonoff (eds. M.A. Dandamayev, Postgate, J.N. and Diakonov, I.M.). Warminster: Aris and Phillips. pp. 285-303.
Pusch, E.B. 1990. Metallverarbeitende werkstatten der fruhen Ramessidenzeit in Qantir-Piramesse/Nord. Agypten und Levante, I: 75-113.
Raven, M.J. 1992. A catalogue project of bronzes in Leiden. Atti VI Congresso Internazionale di Egittologia, Vol i. Turin: International Association of Egyptologists, pp. 529-34.
Ray, J.D. 1972. Two inscribed objects in the Fitzwilliam Museum, Cambridge. JEA, 58: 247-53.
Riederer, J. 1978a. Die datierung Aegyptischer bronzehohlguesse
mit hilfe der thermolumineszenz-analyse. SAK, 6: 163-8.
1978b. Die naturwissenschaftliche Untersuchung der Bronzen des Agyptischen Museums Preussischer Kulturbesitz in Berlin. Berliner Beitrage zur Archtiometrie, 3: 5-42.
1981. Metal analysis of Egyptian bronzes. Revue d’Archaeometrie, 3: 239-43.
1982. Die naturwissenschaftliche Untersuchung der Staatlichen Samrnlung Agyptischer Kunst in Munchen. Berliner Beitrtige zur Archtiometrie, 7: 5-34.
1983. Metallanalysen agyptischen Statuetten des Kestner-Museums. Berliner Beitrage zur Archaometrie, 8: 5-17.
1984. Die naturwissenschaftliche Untersuchung der Agyptischen Bronzen des Pelizaeus-Museums in Hildesheim. Berliner Beitrtige zur Archaometrie, 9: 5-16.
1988. Metallanalysen agyptischen Bronzestatuetten aus Deutschen Museen. Berliner Beitrage zur Archaometrie, 10: 5-20.
Roeder,G. 1956. Agyptische Bronzefiguren. 2 vols. Berlin: Staatliche Museen zu Berlin.
de la Roque, F.B, Contenau, G and Chapouthier, F. 1953. Le &tsar de Tod. Cairo: IFAO.
Rothenberg, B. 1972. Timna. London: Thames and Hudson.
Russmann, E.R. 1981. An Egyptian royal statuette of the eighth century BC. In Studies in Ancient Egypt, the Aegean, and the Sudan: Essays in Honour of Dows Dunham. (eds. W.K. Simpson and W.M. Davis) Boston MA: MFA, pp. 149-56.
Sabet, A.H., Tsogoev, V.B. Bordonosov, V.B., Baburin, L.M., Zalata, A.A. and Fransis, M.H. 1976a. On gold mineralisation in the Eastern Desert of Egypt. Annals of the Geological Survey of Egypt, 6: 201-12.
Sabet, A.H., Bessonenko, V.V. and Mesiha. A.W. 1976b. On cinnabar findings in the Eastern Desert of Egypt. Annals of the Geological Survey of Egypt, 6: 213-21.
Sabet, A.H., Tsogoev, V.B., Shibanin, S.P., el-Kadi, M.B. and Awad, S. 1976c. The placer tin-deposits of Igla, Aby Dabbab and Nuweib. Annals of the Geological Survey of Egypt, 6: 169- 80.
Scheel, B. 1989. Egyptian Metalworking and Tools. Aylesbury: Shire Egyptology.
Schorsch, D. 1988. Technical examinations of ancient Egyptian theriomorphic hollow cast bronzes. In Conservation of Ancient Egyptian Materials, (Preprints of the conference organised by the United Kingdom Institute for Conservation, Archaeology Section, held at Bristol, 15-16 December 1988 (eds. S.C. Watkins and C.E. Browne). London: UKIC, pp. 41-50.
1992. Copper ewers of Early Dynastic and Old Kingdom Egypt – an investigation of the art of smithing in antiquity, MDAIK, 48: 45-159-
Schoske, S. and Wildung, D. 1992. Gott und G6tter im alten Agypten. Mainz: von Zabern [analyses by J. Riederer].
Shaw, C.T. 1995. New Kingdom mining technology with reference to Wadi Arabah. In Proceedings of the First International Conference on Ancient Egyptian Mining and Metallurgy and Conservation of Metallic Artifacts. (10-12 April 1995) (ed. F. A. Esmael). Cairo: SCA, pp. 1-14.
Shearman, F. 1988. An original decorated surface on an Egyptian bronze statuette. In Conservation of Ancient Egyptian Materials (Preprints of the conference organised by the United Kingdom Institute for Conservation, Archaeology Section, held at Bristol, 15-16 December 1988) (eds. S.C. Watkins and C.E. Browne). London: UKIC, pp. 29-34.
Smith. C.S. 1970. An examination of the arsenic-rich coating on a bronze horse from Horortepe. In Application of Science in the Examination of Works of Art, (ed. W.J. Young). Boston: MFA, pp. 96-102.
Stos-Gale, Z. and Gale, N.H. 1981. Sources of galena, lead and silver in Predynastic Egypt. Revue d’Archeometrie, 3 (supplement): 285-96.
Stos-Gale, Z. 1995. The origin of copper metal excavated in elAmarna. In Abstracts of the International Conference on Ancient Egyptian Mining and Metallurgy and Conservation of Metallic Artifacts. (10-12 April 1995). Cairo: Ministry of Culture, Supreme Council of Antiquities, p. 61.
Teeter, E. 1981. Enamelling in ancient Egypt? AJA, 85: 319. Tylecote, R. 1981. From pot bellow to tuyeres. Levant, 13: 107-18.
Page 176
Vandier, J. 1968. La vie des musees – nouvelles acquisitions, Musee des Louvre, department des antiquites egyptiennes. Revue du Louvre, 2:105-8.
Vassilika, E. 1997. Egyptian bronze sculpture before the Late Period. Chief of Seers, Egyptian Studies in Memory of Cyril Aldred (eds. E. Goring, C.N. Reeves and J. Ruffle). tendon: KPI, pp. 291-302.
Vercoutter, J. 1959. The gold of Kush. Kush,7: 120-53.
Vitruvius see Morgan 1914.
Wainright, G.A. 1934. The occurence of copper and tin near Byblos. JEA, 20: 29-32.
1943-44. Egyptian bronze making. Antiquity, 17: 96-8 and 18: 100-2.
1944.Reldimire’s metal-workers. Man, 44: 94-8.
Weill, A.R. 1951. Un probleme de metallurgie archeologique: examen aux rayons X d’un objet egyptien an electrum. Revue de Metallurgic , 48: 97-104.
Weinstein, J. 1974. A fifth dynasty reference to annealing. JARCE, II: 23-5.
Weser, U. 1987. Biochemical basis of the use of copper in ancient Egyptian and Roman medicine. In Recent Advances in the Conservation and Analysis of Artifacts (ed. J. Black). London:
Summer Schools Press, pp. 189-94.
Williams, A.R. and Maxwell-Hyslop, K.R. 1976. Ancient steel from Egypt. JAS, 3/4: 283-305.
Williams, C.R. 1919. A bronze figure of Horus in its original mold. New York Historical Society Quarterly Bulletin, April 1919: 3-7.
1924. Catalogue of Egyptian Antiquities, Numbers 1-6o. Gold and Silver Jewelry and Related Objects. New York: New York Historical Society.
Williams, D. and Ogden, J.M. 1994. Greek Gold: Jewellery of the Classical World. London: BMP.
Winlock, H.E. 1936. An Egyptian flower bowl. Metropolitan Museum Studies, 5/2: 147-56.
Yener, K.A., Ozbal, H., Kaptan, E., Necip, N.A. and Goodway, M. 1989. Kestel: an early Bronze Age source of tin ore in the Taurus Mountains, Turkey. Science 244,4901: 200-3.
Young, E. 1959. Note on a hitherto unknown technique in Egyptian bronze working. JEA, 45:104-6.
Yoyotte, J. (ed.), 1987. Tanis, l’or des pharaons. Paris: Association Francaise d’Action Artistique.
Ziegler, C. 1988. Jeune pharaon presentant l’image de la deese Maat. Revue du Louvre, 3: 181-5.